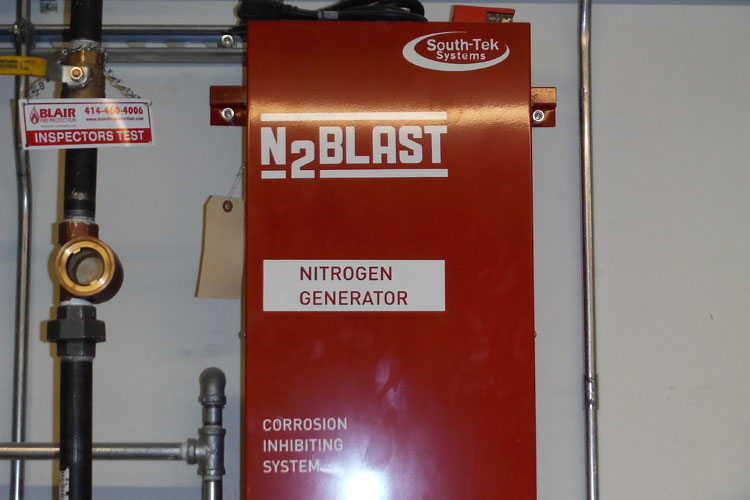
Article and photos by Gregory Havel, except where noted
Corrosion in automatic fire sprinkler systems is a concern to those who design, install, and maintain these systems. The black, foul-smelling water that is sometimes discharged from sprinkler systems during flushing and flow testing is the result of corrosion of the steel by oxygenated water.
This corrosion can be a general surface corrosion which is active only when fresh oxygenated water is introduced into the system and remains until the oxygen in the water is depleted. It may also be localized, forming pits in the steel sprinkler piping that are covered by heavy deposits of iron oxide and other minerals (Photo 1) inside the pipe. The pits will eventually cause leaks. The mineral deposits will restrict water flow during system tests and when sprinkler heads are fused from heat or fire.
(1) Photo by Mr pantswearer, found on Wikimedia Commons.
Corrosion is not only a problem in wet-pipe sprinkler systems. It can also cause serious problems in dry-pipe systems.
A dry-pipe system does not contain water most of the time, since it is designed to be used in areas where temperatures may fall below freezing. The system uses a dry-pipe valve which is held closed against water flow by air pressure in the sprinkler piping that is maintained by an air compressor. When one or more sprinkler heads fuse due to a fire, the air compressor is no longer able to maintain the required air pressure in the sprinkler piping; the dry-pipe valve opens; the system is filled with water; and water discharges from the fused heads.
In a sealed system like this, corrosion is often assumed to be minimal because the system is sealed, and any corrosion will stop when the oxygen runs out. However, the air that is periodically supplied to the system by the air compressor contains both oxygen and moisture. Oxidation (rusting) in a dry-pipe system can be more rapid than in a wet-pipe system.
One method of corrosion control in dry-pipe sprinkler systems is to install a refrigerated air dryer between the air compressor’s tank and the dry-pipe system. This method cools the compressed air below its dew point and permits most of the moisture in the air to condense and be removed from the air before it enters the system. Although this method does reduce corrosion, it also continues to introduce a supply of fresh oxygen into the system.
A more recent development in the corrosion protection of these systems is the use of dry nitrogen in place of compressed air to maintain pressure in the dry pipe system.
Tanks of compressed nitrogen gas can be used in place of compressed air. However, this kind of system requires close monitoring to ensure that the pressure in the nitrogen tanks is not depleted. If this happens, the dry-pipe valve will open and permit the dry-pipe system to be flooded with water. This will have to be drained, the system serviced, and the nitrogen source replenished before the system freezes.
(2)
The most recent development is the use of a “nitrogen generator” (Photo 2) rather than tanks of nitrogen gas. This nitrogen generator is similar in function to the “oxygen concentrator” that is frequently used by persons with chronic respiratory diseases, except that the discharges are reversed. The oxygen concentrator stores the oxygen for use by the patient and discharges the nitrogen and other inert gases as waste to the atmosphere. The nitrogen generator stores the nitrogen and other inert gases for use and discharges the oxygen and moisture to the atmosphere.
(3)
Photo 3 shows a nitrogen generator connected to a dry-pipe sprinkler system.
1. The air compressor [1] is turned on and off by a pressure switch in response to the pressure in the generator system.
2. The compressed air is stored in a compressed air tank [2] with an automatic moisture drain to prevent the air tank from filling with condensation.
3. As the compressed air is needed to replenish the system, it passes through a pipe to the nitrogen generator [3], where oxygen and moisture are removed
4. The dry nitrogen passes through a pipe to the nitrogen tank [4], where it is stored under pressure until it is needed by the dry-pipe system.
5. The nitrogen flows through a pipe [5] to the dry-pipe system, where it is used to maintain the pressure needed to hold the dry-pipe valve closed.
The nitrogen generator system replaces the air compressor often associated with dry-pipe systems; eliminates the introduction of oxygen and moisture into the dry-pipe system with compressed air; and eliminates the need for monitoring the status of a manifold of nitrogen tanks to supply the pressure in the dry pipe.
Nitrogen generators are being installed on both new dry-pipe sprinkler systems and on existing systems that are subject to corrosion.
Fire department personnel who are responsible for inspecting occupancies with these nitrogen systems must be familiar with them. Inspectors must be sure to check the maintenance records on these systems, much as they do for sprinkler system flow tests, fire pumps and other related equipment.
For more information on corrosion, search the Internet for “corrosion” and “corrosion protection.”
For more information on nitrogen generators, search the Interne for “nitrogen generator”.
For the automatic fire sprinkler system code requirements on use of nitrogen generators on dry-pipe systems, see NFPA 13 Installation of Sprinkler Systems, 2016 edition, especially Section 7.2.6.8; Section 7.8.2.7; and Section A.7.2.6.8.1. Your fire prevention bureau or local fire training school may have a subscription to the NFPA Codes and Standards that can be available for your use. Or, you can use the NFPA Codes and Standards “Free Access,” available with a free log-in at https://www.nfpa.org/freeaccess.
Download this article as a PDF HERE (815 KB).
Gregory Havel is a member of the Town of Burlington (WI) Fire Department; retired deputy chief and training officer; and a 35-year veteran of the fire service. He is a Wisconsin-certified fire instructor II, fire officer II, and fire inspector; an adjunct instructor in fire service programs at Gateway Technical College; and safety director for Scherrer Construction Co., Inc. Havel has a bachelor’s degree from St. Norbert College; has more than 35 years of experience in facilities management and building construction; and has presented classes at FDIC International. This year ihe is presenting on “Building Construction and Fire Behavior.”
MORE CONSTRUCTION CONCERNS