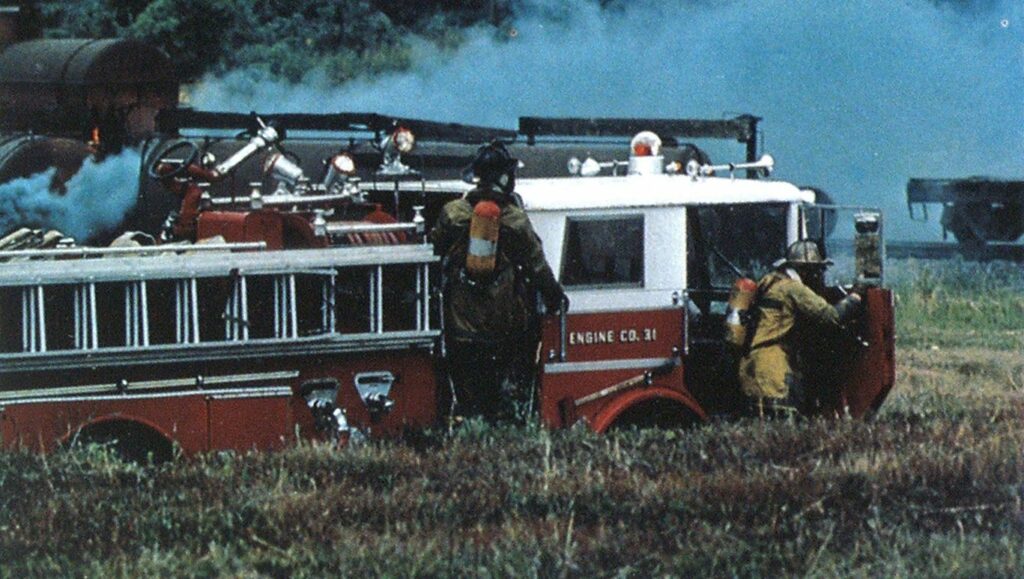
Haz-Mat Accidents on the Railroad: Know What to Do When They Occur
features

—photo by Andy Levy.


As major carriers of hazardous materials, railroads are a concern to emergency response groups. They are found everywhere and they have a very high incident rate. The quantities carried are large, providing the potential for a major leak, spill, fire or explosion.
Incidents may be caused by failures in equipment, track and roadbed deterioration, and human error or sabotage. The railroads have started track improvement programs with the use of ribbon rails, infrared detectors for cracks, and other track-testing equipment. Federal regulations have required the removal of carbon steel wheels from tank cars. Changes in single-shell pressurized-gas cars include shelf couplings, head shields for tank ends, and thermal coatings or outer jackets. Further changes are being recommended for hazardous material cars.
Strategy vs. tactics
Emergency response actions are generally divided into strategy (preparation before the incident) and tactics (operations to control the situation when it occurs). The major control objective is to take those actions necessary to bring the incident to a successful conclusion, keeping in mind the goal of protecting lives and property with the resources available in an acceptable time frame and in a safe, effective manner. Each incident, of course, will be different.
The strategy for a rail incident begins with planning and includes all items that must be covered to prepare for a transportation incident. The plan should consider:
- Routing of the railroad in the local area.
- Commodities that normally move through the region.
- Response routes and accessibility to the track.
- Considerations for safe approach.
- Obstructions that will be encountered.
- Topography along railroad rightof-way.
- Exposures (people, property, environment, air, ground surface water, water table).
- Evacuation problems and corridors.
- Extinguishing agents or neutralizers required.
- Spill or leak control requirements.
- Railyard problems (see Fire Engineering, August 1979, page 112).
- Technical assistance.
- Resources available (what, where, how obtained).

Photo by William Cooper

With an adequate plan, standard operation procedures (SOP) can be developed for the anticipated incidents. It is especially important to work out how water, if required, will be supplied to the incident site. In many areas this will require considerable work to develop relays—through hose lines or with tank vehicles—to provide the quantities required for a multiple railcar derailment involving fire.
Plans should be made for special operations required by railroads such as dome leaks, bottom unloading outlet problems, diesel locomotive fires, punctures and purging.
Command post
Also, SOPs must be completed for the establishment and running of a command post. Due to the hazardous materials and quantities shipped by rail the command post must be prepared for the unusual. This will require adequate personnel, resources and training.
Communications during a hazardous materials incident are vital. Lines must be kept open for clear, concise, exact information to flow to and from the command post. During a recent incident, the state police assisting a local police agency stopped traffic on a major expressway. They further halted emergency response apparatus and would not allow them to proceed to the incident scene. It took some time for communications to travel from the command post to the governor’s office to the state police headquarters to the field to remove the roadblock to responding mutual aid.
The fire service must learn to communicate with the other agencies it will turn to for technical assistance and information. The communication problem extends all the way down to basic fireground communications. Personnel on the scene must be cautioned to spell chemical names, indicate if they are more than one word, and have names spelled back to assure correct transmission.
The development of a command post strategy will improve efficiency of the operations when an incident occurs. The staff assembled will vary with the size of the situation. The location may depend on staff size, weather conditions and vehicles or buildings available. A large area with room for parking, a staging area, and a decontamination zone may be desirable. It is vital the command post be established early, the location announced and the site clearly marked.
The support functions that must be provided by the command post staff include safety, extinguishing or control agents, communications, supply, medical, and public information. Desirable of necessary equipment includes telephones and radios; weather instrumentation; lighting; standard office secretarial materials; chemical reference books and data sheets; planning, medical facility and evacuation documents; maps of water systems, sewers, traffic routes, evacuation routes, topograpy, utilities and staging areas; and aerial photographs. Incident record sheets will be helpful, including personnel exposure forms.
Command authority
A major question must be determined during strategic planning: Who is in charge? This should be determined for both initial and subsequent operations.
With the event of the national contingency plan of the federal government, several people will arrive on the scene, including an on-scene coordinator (OSC), and possibly the regional response team, which will coordinate with the national response team. The OSC will be from the U.S. Coast Guard or the Environmental Protection Agency. Representatives of manufacturers, shippers, industrial groups and various federal agencies will also arrive on the scene. All these people will be offering advice and suggestions. Strong pressures may be brought to bear on the local fire officer in charge. Depending on the legalities, the ranking fire officer should remain the incident commander, since he or she is responsible for the safety of the lives and property of the local community.
Once an incident has occurred, specific tactics must be started toward control.
Safety of personnel
The first tactical consideration is the safety of personnel working in the area. This starts with the safety officer assuring that all exposed skin is covered. When using fire service protective clothing, exposed wrists must be covered, earlaps must be put down, collars put up, positive-pressure SCBA donned, and ankles, waist and wrists taped to exclude vapors. Since some products permeate synthetic rubber, proper gloves must be worn such as high-density polyethylene or Vi ton. With many products special protective clothing designed for them will be necessary to avoid penetration by liquids or vapors. The fire department should know where to obtain proper protective clothing for an emergency if it is not currently available.
Approach size-up: During the initial response to a train incident an approach size-up is necessary. This will ensure safe positioning without endangering the emergency response personnel This must include determining whether hazardous materials are involved and the nature of the problem, whether a liquid spill, a vapor leak, a fire, an explosion, or the potential because of a deteriorating situation.
As much information as possible should be obtained while en route. It may be necessary to change the response route based on information received or to stop some distance from the site and don positive-pressure SCBA before proceeding on foot, rather than riding into an ignition source.
Factors that must be considered are the wind direction and velocity, the gradient of the area, the hazards of the materials involved (if known), the positions of the hazardous material containers and where the response route will take the companies in relation to the incident site. Getting in close to perform a good tactical size-up is important but cannot be overshadowed by the need to protect the responding personnel. This is a time when the use of binoculars is warranted. Another concern during approach is placing companies where they have access to available water supplies and are in a position to protect exposures.
Tactical size-up: Once in a position to safely observe the situation, the officer in charge can begin the decisionmaking process. This begins with a formal determination of the problem, if not already known. Then a tactical size-up begins, including information gathering and evaluation of data. There will be little time to do this if there is a large flowing leak, a moving spill or a rapidly spreading fire. Remember that with the changes in the former single-shell flammable gas tank cars the possibility of a BLEVE at a derailment has been reduced. The evaluation of the data must lead to the selection of one of the possible alternative courses of action.
Among the items reviewed in data gathering and evaluation are:
- Identification of the material.
- Quantities (number and size of containers).
- Life safety considerations.
- Location, terrain and exposures.
- Position of containers.
- Construction and condition.
- Time and weather condition.
- Extinguishing agents.
- Attack positions, obstructions and accessibility.
- Manpower and equipment.
- Outside help available.
It is not within the scope of this article to detail each of these items. It is necessary, however, to briefly comment on some.
Identifying materials
Identification of hazardous materials in rail transportation is changing with the new DOT placarding regulations. Where former placards generally provided only a warning rather than identification, the new system with numbers on the placard or adjacent to it should lead to positive identification either by on-site reference to the DOT Hazardous Materials 1980 Emergency Response Guidebook (DOT P 5800.2) or by relaying the number to a technical assistance source. Also the United Nations class will be denoted by the small numeral at the bottom of the placard. Many products are required to have the product name stenciled on the side of the car. This is done for over 40 commodities.
Perhaps the most positive identification can be made from the shipping papers. The involved cars numbered from either side or end must be obtained and matched to the proper shipping documents. The train conductor has the waybills that provide the product name (soon: the product identification number as on the placard), the shipper’s name and the destination. The conductor may also have a consist, wheel report or switch ticket that can provide information. Some railroads provide detailed computer-printed hazardous material information including car number, position in the train and action to be taken for fires and spills with the consist.
Fire departments along railroads should check with each rail company to determine its procedure and obtain a sample of the shipping document for familiarization and training. A call to the railroad dispatcher with the car number will also bring identification assistance. Pertinent railroad contact numbers should be available.
Generally, the shipping papers are in the train caboose; however, some railroads carry them in the locomotive, and others in both locations. Again, check with the local railroad. The papers for cars in a classification yard will be found in the freight office or with the yardmaster.
Exposures
It must be pointed out that exposures to hazardous materials go beyond those normally considered in structural fire fighting. Exposures include: open bodies of water, water tables, sewers, the soil, air, anything that could be affected by fly ash downwind, buildings, other rail cars and people in the area, including all emergency response personnel. Personal exposure can come through the eyes, from radiant heat, by skin absorption, ingestion or inhalation. This requires a broadening of our actions to protect exposures.
The concept of time must be broadened also. Not only is the time of the incident important but also response time, time to initiate actions, length of time the fire has been burning or leak has been flowing, duration of flame impingement, how long it will take additional resources to arrive and be placed in service, and the time to provide adequate extinguishing or controlling agents.

Extinguishing agents
Train derailments—due to the large volumes of materials carried, often in bulk shipments, and the number of cars that can be involved—will require large volumes of extinguishing agents. This may be water or special agents. One recommendation for water has been 500 gpm per tank car.
Polar solvents (water soluble) materials will require alcohol-type foam. Regular, fluoroprotein and AFFF foams may be necessary in large quantities for flammable or combustible liquid fires. Other agents and foam may be required to control spills and to control the vapors from a diked spill, including neutralizers, inhibitors or dispersants. Any planning should include provisions for extinguishing and control agents and their delivery to the often-remote railroad right-of-way.
The manpower consideration is important because it affects the delivery of the extinguishing agent or the control of spills. The bottom line is whether there is sufficient manpower available for the required spill control operations or to move adequate agent to the incident. This manpower requirement may be beyond the fire department’s resources and include such people as heavy equipment operators or water department personnel.
A major area to evaluate is the condition of the car or cars, based on the stresses to which they are being subjected. Thermal stress from flame impingement is generally noticed first. However, the outside air temperature change influenced the internal pressure of a rail car sufficiently at Waverly, Tenn., to cause a spot damaged many hours earlier to completely fail without warning. Chemical stress could also occur during a fire or spill and weaken the shell, leading to a breach.
Mechanical damage happening during the incident is difficult to assess. When examining a damaged tank, watch for scores or gouges in conjunction with a dent, cracks at the crown radius of a dent, or cracked or gouged welds. Longitudinal dents with a radius of curvature of 4 inches or less that include cracks, scores or gouges, or cross a weld must be considered dangerous. Seek expert technical assistance.
Decision making
Once the data has been gathered and evaluated, the alternatives must be reviewed. At all times the incident commander must anticipate even the unlikely event that can occur at a hazardous materials accident. The major question that must be asked with each alternative is how it will affect the outcome. In some cases the alternative of doing nothing at all is most logical.
Too many fire service people select an OSRIC type of response—Oh Safe and Rush in Close. This alternative can be unwise if identification and condition evaluation have not been performed. Other alternatives are: confinement, especially with liquid spills, holding them to the smallest possible area; control for liquid or gas leaks; extinguishment; withdrawal; or a vent-and-burn operation.
Evacuation
Evacuation may be necessary for the safety of those in the area. While the immediate area will be evacuated by the fire department, agreements should be made in advance with other agencies for completing the evacuation for a minimum distance of 1 mile. There are many problems to overcome in a densely populated area. The details of manpower, means of alerting, traffic control and routes, shelters, and movement of the elderly, invalids and hospital patients are only a few. The massive evacuation of Mississauga, Canada, can be studied for greater insight.
Confinement and control may depend upon the quantity involved and the rate of leakage. Spill confinement measures may include dikes, dams and channels covering the product with the correct type of foam, whether AFFF, regular and fluoroprotein for flammable and combustible liquids, high expansion for corrosives and poisons, and alcohol-type for polar solvents. Controlling small leaks may be handled with numerous plugs or a Chlorine “C” kit.
Extinguishment requires knowledge of the product, adequate quantities of agent, equipment to deliver it with, the time and manpower to safely initiate the operations, sufficient master stream devices for cooling (possibly unmanned or from protected locations) and the procedures to develop the minimum 500 gpm per tank car.
Withdrawal of all operating emergency response personnel from the scene is necessary when the situation deteriorates or it is deemed too dangerous to approach the scene. All personnel in a 2500-foot radius should be removed and control lines established.
Rapid termination
A new procedure recently introduced by the EPA is called vent and burn. This operation for burning tank cars calls for placing explosive charges on the tank and detonating them. The advantage of this is the immediate removal of the hazardous commodity. Local incident commanders may want to consider exposures and liabilities before consenting to this operation in their community. The report from this operation at Molino, Fla., states that several tanks were destroyed in a rural area 2 miles from the town rather than maintain a week-long evacuation while the tanks burned out. The fireball was 3000 feet high and a quarter-mile in diameter.
From the available alternative operations, the incident commander must select and implement a plan of action. The safest, most feasible and expedient alternative based on evaluation of the situation, resources and the time constraints should be selected.
The scene commander should seek technical advice if necessary but may need to temper the decision with experience and knowledge of local problems. The National Transportation Safety Board reported recently “….The Somerville accident was the latest in a series of hazardous material spills with which local safety officials have had to cope by trial and error.” Guidelines and technical advice from the federal government, the shipper and others were shown in Somerville to be inadequate, inconsistent, and confusing. (See Fire Engineering, June 1981, p. 11.)
The plan of action must be monitored and changed if necessary. Those officers in charge of the various sectors must report to the incident commander on the progress or lack of it. The plan must be altered-if problems develop. Timely reevaluations will be necessary based on the feedback coming into the command post.
Post-incident operations
Once the incident has been secured, the fire department may have to assist in clean-up operations. They may be called upon for manpower, water supply, ventilation equipment for purging, or exposure protection. Although the fire department is not responsible for clean-up, community safety must be considered.
Decontamination of fire department equipment, apparatus and personnel may be required. This could include on-site washdown and capturing the runoff for proper disposal. Proper solutions for decontamination may have to be prepared based on advice from the manufacturer. Enclosures for containment of initial washdown runoff, containers for discarded protective clothing, showers for personnel, and fresh clothes could be necessary at the incident site.
A final report should be prepared and a critique held. This will enable those within and outside of the department to benefit from the experience. All actions should be detailed in case of subsequent investigations or litigations. Those actions that were favorable should be commended and considered for inclusion in hazardous material operating procedures. These operations that could be improved should be discussed and recommendations should be made for future incidents. Faulty operations should be pointed out, not in a sense of criticism but to prevent others from making the same mistakes during other incidents.