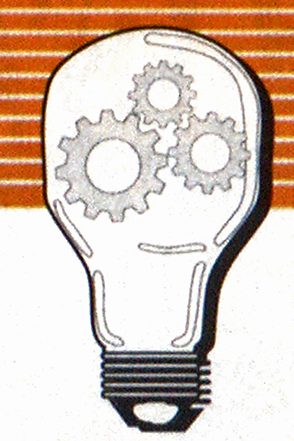
RESCUE AIR SYSTEM FOR HIGH-RISES
INNOVATIONS: HOMEGROWN

Emergencies involving high-rise buildings create demands that often exceed the resources of a fire department. The resource most commonly affected is personnel.
Redwood City, situated 20 miles south of San Francisco, has a population of approximately 67,000. By the end of this year, the city will have four or possibly more high-rises, and the demand for additional bigger and higher buildings is growing.
The Redwood City Fire Department began preparing for personnel problems related to high-rise emergencies when it adopted in 1986 the “Rescue Air System,” also referred to as the Rescue Air Manifold or the Remote Air Fill System. The concept involves installing a system of vertical tubing that runs inside the walls of the building, making it possible for firefighters and other emergency personnel to refill their self-contained breathing bottles w-ith fresh air without having to leave the building. This system significantly reduces or virtually eliminates the need to carry full air bottles up to the staging area from the air-filling station on the ground floor and to bring empty bottles down from the staging area.
THE SYSTEM’S DESIGN
The system consists of the following:
- A ground-level connection station. It may be connected to a portable or stationary reliable air supply. This station includes a shutoff valve, a pressure gauge, and a female pressure connection on a length of high-pressure hose installed in a lockable enclosure that is protected from the weather, if the enclosure cannot be located in a protected area, it must be weatherproof. The high-pressure hose must be long enough to reach the portable high-pressure supply vehicle and must incorporate a safety cable and snap to protect against hose rupture.
Whenever possible, the ground floor station should be located upwind to reduce the possibility of air contamination from the surrounding atmosphere. It must be located in an area that is easily accessed by the fire department’s portable high-pressure supply vehicle and in a location that
Will be a safe staging area for supporting the firefighting activity under all conditions. If no sufficiently protected area exists at the building itself, then a remote station location must be used and the pressure piping run underground in a protected raceway or conduit to the building.
The ground floor station supplies clean air to the other stations by means of stainless steel tubing approximately ½ inch in diameter, depending on the overall size of the system.
- Intermediate fill stations. These include a fill shutoff valve, a pressure gauge, a quick disconnect-type male pressure connection on a length of high-pressure hose, a pressure bleed
- valve, and an isolation valve—all installed in a lockable enclosure. The high-pressure hose must be long enough to allow convenient connection to the firefighter’s breathing apparatus. A safety cable and springloaded snap are fastened to the highpressure hose to protect against hose rupture. The isolation valve is arranged so that when it is closed, all stations above the valve are sealed out of the circuit.

REDWOOD CITY FIRE DEPARTMENT Hi-Rise Remote Air Fill
Firefighters fill bottles from fill stations located on every odd-numbered floor vestibule (staging).
Adapted from a drawing by G. Belanger.
The intermediate fill stations should be located so that the firefighter can refill his breathing system within two floors of the fire. There is no reason to have a fill station on the topmost floor of the building, so it is recommended that a station be established on the second from the highest floor and then on every other floor below that until the ground floor, where, again, a station is not required, since the ground floor is close to the ground level connection station. The stations may be established every third floor if the department prefers. The stations should be close to, but not inside, the main exit stairwells to avoid congestion during emergency evacuation.
In buildings wider than 200 feet and served by more than one main stairwell, it is recommended that stations be located at each end of the building.
The lowest intermediate filling stations are connected by horizontal stainless steel tubing, and the other filling stations inside the building are connected by a vertical supply run. High-pressure tubing must be adequately supported (pipe hangers every 48 inches for horizontal runs) and protected from rubbing against solid objects with rubber, plastic, or fabric materials.
MATERIALS AND TESTING
The Rescue Air System and its components are bench-tested at 5,000 psi working pressure. All components should meet the requirements of ANSI B31 and ASME Section II1V codes. This requires a safety factor of 4 for all pressurized materials. High-quality commercially available components should be used. All materials used in inaccessible areas, such as piping, should be corrosion-resistant steel such as 304 stainless steel or better. Materials used in accessible areas must be suitable for containing highpressure, oil-free air. The internal surfaces of all components must be free of contamination, especially hydrocarbons, so that the air contained within meets grade D breathing air requirements. Where stainless steel components are joined to other stainless steel components, provisions must be made to prevent galling.

When installed, the entire system is hydro tested at the initial installations and after any major alteration of the system including exposure to fire for pressures equivalent to one and onehalf times the normal working pressure. After the system has been aired and dried, an air-pressure test equivalent to the highest working pressure-plus a 2 percent gauge accuracy allowance (plus or minus 100 psi) —is conducted. After all tests have been successfully completed, the system is placed in service with approximately 150 psi positive pressure to reduce the remote possibility of contamination.
The cost of the system varies with size, design, and configuration. A ballpark figure would be around $ 1,800 to S2,100 per station including installation.
The system is simple in design and easy to install and operate. Firefighters in Redwood City and neighboring jurisdictions, although skeptical about it at first, now recognize its immense value, realizing that climbing stairs to exchange air bottles is not the most intelligent way to use personnel, who are valuable and often scarce during these emergencies.
By the end of 1991, Redwood City will have seven air systems in place. All were installed during the buildings’ construction phases. Because of its simplicity and ease of installation, however, a Rescue Air System very easily could be retrofitted in existing buildings.
The Rescue Air System was designed by John Below, P.E., chief engineer for a major producer of highpressure breathing air compressors in the San Francisco area. He, with Ralph Tiemann (system patent licensee) and personnel from our department, supervised the installation of the systems.
Additional information about the Rescue Air System is available from Ralph Tiemann Enterprises, 531 Cherry Street, Petaluma, CA 94951, (707) 763-3330.