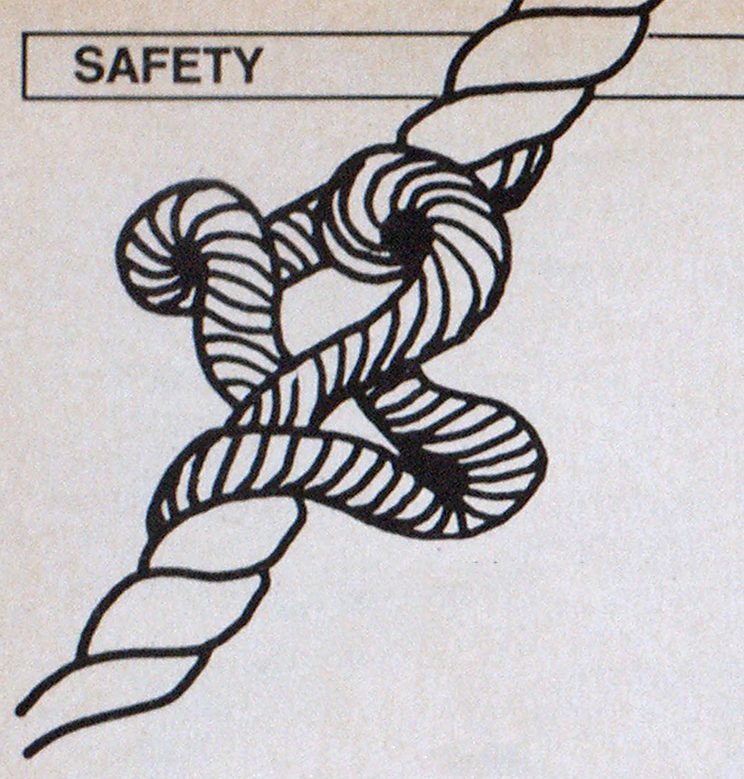
SELECTING ROPE FOR FIRE AND RESCUE OPERATIONS
SAFETY
Because of the critical lifesaving situations in which fire fighters use rope, it is important to know not only the various ways of using ropes, but also the physical properties of rope itself.
It is not in the best interest of the fire service to purchase life-saving rope made of manila (natural) fiber. After exposure to air and light, manila fiber deteriorates beyond safe limits for life-saving uses. Also, size for size, manila is not as strong as nylon or polyester. These are only two of many reasons why manila is a poor choice for a lifeline.
Life-saving rope should be made of nylon or polyester. The construction can be three-strand twisted, braided, kernmantle or plaited.
For best overall use of a rope in a single deployment system, the diameter of the rope should be from 9/16 to 3/4 -inch. The present recommended minimum breaking strength of a life-saving rope is 8000 pounds. It is recommended, however, that the minimum breaking strength of these ropes be increased to 10,000 or 11,000 pounds to ensure a breaking strength of at least 8000 pounds after a rope has been used, kept in service, and used again a year or so later. The rope must be compatible for use with its related equipment; for example, kernmantle rope kinks severely when used with a pompier hook, while a twisted rope’s performance depends on the lay of the rope and the method of applying the turns of rope onto the hook.
Synthetic ropes are made of continuous filaments which are thousands of yards long and thinner than a hair. Noncontinuous filaments (natural fibers) are only several inches long and therefore not used for cordage fiber. However, rope constructed of continuous filaments does not mean knot-free rope. To make knot-free rope, knots must be cut out of the yarn during rope fabrication, and construction is continued by overlapping the severed yarn. It is impractical and probably impossible to purchase knot-free rope.
Twisted rope construction
Briefly, a twisted rope is fabricated as follows. Nylon fiber is prepared by pumping molten nylon through very small holes. Upon emerging, the fine filaments are solidified by cooling and wound onto bobbins The filaments are approximately 35,000 yards long and, depending on an order of rope, as many as 140 filaments or more are lightly twisted into a strand that is termed an “end.” As ends are wound onto a spool or tube, as many as three knots can be included because, where an end runs out during winding, a knot is made to join another end to it and the winding is continued until the tube is full. A cordage finish is applied to the fibers to provide the nylon with abrasion resistance and some additional strength. Then the ends are delivered to a rope manufacturer on a large spool called a “beam.” A beam of 168 individual ends, wound side by side, totalling 25,000 yards of yarn, would be used to fabricate a 9/16-inch three-strand twisted rope. A twisted, balanced rope is manufactured as follows: The ends are unwound simultaneously in sets of fours and then wound onto bobbins as a single yarn with a “Z” twist right lay. Four single yarns are then wound onto a tube in the form of plied yarn with an “S” twist left lay. Thirteen tubes of plied yarns are then spun or formed into a single strand with a “Z” twist and wound onto a spool. Three strands are spun or laid into a rope with an “S” twist. The rope is then stabilized or heat set at a temperature of 180 degrees for two minutes. Finally, the rope is cut to length and prepared for shipping.
Ends are not mentioned in rope specifications, but knotless singles yarns, plied yarns and strands are specified The knots used to join the ends do not affect the strength of the finished rope. However, knots tied in singles or plied yarns do affect a rope’s strength and the rope must not be accepted.
Selection of a nylon or polyester fiber is not very difficult when both synthetics are understood.
Polyester rope resists abrasion better than nylon.
Both synthetics can absorb 20 percent of the weight of the rope in water. Nylon can lose up to 15 percent of its strength when soaked in water for approximately 24 hours. After drying, the full strength of the rope will return. Repeated soaking or washing will leach out the cordage finish. A 3/4-inch nylon rope is approximately 12 percent stronger than a comparable polyester rope Therefore, comparing the wet strength of nylon rope to a polyester rope is insignificant, because both ropes would be about equal in strength
The dielectric properties of both ropes are also about equal. Alkalies such as soot and ash reduce the strength (if polyester and the resulting strength loss is permanent. The loss in strength is not sudden Affected rope fibers would deteriorate in the same way as would manila fibers.
Application considerations
When selecting fiber, the intended use of the rope should also be considered. Life-saving rope may be used in either a vertical or horizontal deployment
A rope intended basically for a vertical deployment more likely will be subjec ted to shock loading, as when making a rescue pickup of a victim Such a rope should be made of nylon with elongation of approximately 40 percent at the breaking strength of the rope. When suddenly loaded, this dynamic rope will absorb the energy of the impact force through elasticity. A nylon rope with a static construction and approximately 20 percent elongation at the breaking strength of the rope will absorb some energy while the remaining force will be transmitted to the person attached to the rope. Polyester rope does not provide relief of any of the impact force to the person attached to the rope.
A rope intended basically for horizontal deployment, such as a traverse system, should have little stretch. This rope can be made of nylon or polyester.
When a dynamic rope reaches total stretch and breaks, the “snap-back” effect causes serious injury and death to people in the path of the recoiling rope. When large-diameter ropes, such as hawsers, are subjected to breaking strength stress, they break and recoil at speeds of 700 feet per second.
A life-saving rope must not be used for towing or hauling tractors, cars or similar heavy equipment. A life-saving rope is intended to hold the weight of two and possibly three people, as has been the experience of some New York fire fighters. In such a situation, the persons that would receive the most serious injury due to a rope failure are those who are supported in suspension by the rope Any nylon rope has the potential to snap back should the rope be stressed to its breaking strength.

After the fatal accident to two New York fire lighters in lune 1980, when a 1/2-inch nylon rope broke, the New York City Fire Department made a search for the best rope available for use as a life-saving rope. The best rope on the market could not meet NYFD demands. One rope manutacturer devoted specific attention to the fire department’s needs and. consequently, a rope of special construction was fabricated for the NYFD Other manufacturers could not change their production values to meet these life-saving rope specifications.
Weight support tests
Various ropes made of polyester or nylon were subjected to severe tests at the New York Fire Academy in July 1980. The ropes were of kernmantle (made by domestic and foreign manufacturers), threestrand twisted, plaited, double-braided and braided constructions Although polyester ropes proved to be strong and durable, the elasticity was unsuitable for NYFD purposes During the performance testing of this type rope, a high impact load was absorbed by members who braked sharply while performing a single slide or rappel. Such load absorption is painful and, of course, the impact force is increased when a rescue pickup is made. Therefore, it was decided that nylon rope would be purchased because the rope would be used for vertical deployment 99 percent of the time Testing of polyester rope was discontinued.
To establish a standard of testing, a 1/2-inch nylon twisted rope (the rope that was in use at that time) was subjected to the following test One end of the rope was anchored and the rope laid out horizontally along a deck to the deck’s edge, which was made of steel and approximately 10 feet off the ground. The edge was very rough and the rope was not protected from the edge during the test. Sufficient rope was allowed for the attachment of a 510-pound weight to the free end of the rope, with an additional allowance for 2 feet of slack between the weight and the platform edge.
Using a forklift to support the weight, the weight was made to fall. Five successive drops of the weight were made and the elongation of the rope was measured after each drop while the weight was supported by the rope. After the fifth drop, the total slack in the rope had increased to 8 feet, and so the rope absorbed the impact of the weight falling 8 feet. On the sixth drop the rope broke. Thus, any rope that would be considered for the NYFD life-saving rope would have to survive more than five such drops. It was felt that the weight used was equal to two fully clothed fire fighters supported by a rope at the same time. The total length of the rope was approximately 40 feet in order to simulate the fireground use of the rope as it would be used by NYFD fire fighters.

A 3/8-inch nylon kernmantle rope with a breaking strength of 12,000 pounds survived five drops, at which time the mantle or cover separated where the rope contacted the steel edge. After the fifth drop, the total slack increased to 4 feet. This was a static rope with little elasticity. The rope broke on the sixth drop when the inner fibers contacted the steel edge In this respect, the rope was not better than the 1/2-inch rope which caused the fire fighters’ fatal fall.
An 11-millimeter, mountain-climbing kernmantle rope of dynamic construction also survived five drops and broke on the sixth drop when the inner fibers made contact with the edge. Other kernmantle ropes survived one drop and broke on the second drop after the cover separated. The cover of a kernmantle rope contains 25 percent of the rope’s total strength and the many strands of the core are kept tightly together by the cover. Apparently, when the cover separates at an edge, the core is able to spread out along the edge. This subjects all the strands to a 90-degree bend, causing them to break.
A 5/8-inch double-braided rope proved to be very strong, surviving 10 drops. However, this rope was heavier than desired and kinked severely when used with a pompier hook. The pompier hook has been in use for many years by the NYFD, and all members are well-trained in its use. A change to a figure-eight or other type of hook would require that each member be trained in the use of the new tool. It is not easy to train 11,000 men in a short period of time without the possibility of causing confusion under extremely perilous fireground conditions. Therefore, this rope could not be accepted.
A three-strand twisted, 1/12-inch right lay rope (nylon) with a breaking strength of 10,000 pounds was subjected to the same test. This rope broke on the 15th drop and played through the pompier hook without kinking. The elasticity was equal to the stretch of the 1/2-inch rope. Additional ropes of this type were tested and the problem of kinking developed.
Two ropes were left to hang in a fivestory stairwell overnight with a light weight attached to the end of each rope. It should be mentioned that contrary to previous statements, twisted rope if properly balanced does not spin and untwist in a direction counter to the lay of the rope with a weight attached to the end.
An additional test was made on a 3/8-inch rope with a 510-pound weight attached to the rope’s end. The weight was made to hang free while being supported by approximately 8 feet of rope. The rope did not untwist.
After the ropes hung all night, they were packed clockwise and counterclockwise and played out through a pompier hook with the same result of kinking.
The inherent effect of kinking in twisted rope when used with a pompier-type hook requires that a life-saving rope be packed and used one time before being placed into service. Kinking occurs during the lowering of a person from an elevated area. Therefore, each NYFD life-saving rope is initially used to lower a fire fighter from the roof of a five-story training building. The ope is then coiled into a backpack carrying ase and placed into service.
Plaited rope looks promising
Plaited ropes are of a torque-free, balanced construction and, therefore, do not kink when used with a pompier hook. This rope does not have to be tested prior to being placed into service. These eight-strand ropes are fabricated from two pairs of left lay strands and two pairs of right lay strands. This is not a braided rope, since the strands of a plaited rope are not interwoven as frequently as they are in a braided rope.
The breaking strength of a 9/10-inch plaited rope is approximately 10,000 pounds. A 5/8-inch rope has a breaking strength of approximately 11,000 pounds. Elongation at break is about 50 percent.
The 3/6-inch rope broke on the ninth drop using the 510-pound weight while the 3/8-inch rope broke on the 15th drop. This rope proved to be durable since the breaking strength was 6800 pounds after being used 318 times.
Results of subsequent testing were not as impressive as earlier results. The manufacturer has made adjustments in the fabrication of these ropes in an effort to satisfy NYFD demands. Tests are still being conducted with this rope and it appears to be an excellent choice for use as a lifesaving rope.
A three-strand twisted, 3/4-inch left lay nylon rope with a breaking strength of 11,000 pounds was fabricated for tests. This rope survived 13 drops and did not kink when used with the pompier hook. The rope had to be coiled counterclockwise when it was packed in order to be kink free. This is the rope now used by the NYFD, and has a hardness of 6 pounds which is a soft lay rope.
An additional test was made on this rope to determine its overall ability to withstand shock loading after repeated use. A sample rope was used 101 times for combined sliding, lowering and rescue pickups. The rope was then subjected to the drop tests with the following additions: The rope was fed through a 1 3/4-inch hose; the hose protected the rope at the platform edge, which was now covered with a 90-degree angle iron.
With 2 feet of slack in the rope, the weight was made to drop. After the third drop, one strand was found to be heavily abraded. After the seventh drop, hockles appeared near the knot at the weight. After the ninth drop, a second strand was found to be heavily abraded. Testing continued, occasionally shortening the elongated rope to prevent the weight from touching the ground. After the 20th drop, the abraded strands became severed. The rope finally broke on the 27th drop.
This test was done again at a later date with the same results. During one test, the rope was soaked after the fifth drop and a strand was severed with a knife. The test continued until the 19th drop when a second strand was severed. The rope broke on the 24th drop.
Training ropes
DuPont nylon 707 and Allied nylon 1T81 are filaments that seem to have the best resistance to abrasion during continued use of a rope. After 150 to 4,000 sliding and lowering operations, a laboratory static breaking strength test was made on sample ropes. A twisted rope with an unused strength of 11,000 pounds was used 250 times; it broke at 6500 pounds After 300 uses, the same type of rope broke at 6300 pounds; and after 4 $0 uses, the rope broke at 56,000 pounds.
These tests were made to determine the safe operational use of a rope for training under controlled conditions with a safety net or air-filled mat in position Training ropes should be of the same construction as the life-saving rope. Life-saving rope must be restricted to life-saving use on the fireground or in other emergency conditions. A training rope must be identifiable to avoid the mistake of using it in place of a life-saving rope during emergency conditions. Also, training ropes should not be carried on the apparatus.
Training ropes should be able to withstand 200 operational uses, after which the breaking strength should be at least 5000 pounds Where a single rope system is used for life-saving operations, training sessions should also be held using a single rope and not a two-rope system to avoid confusion of life rope usage. A rope must be protected at the point where it is deployed over an edge during training and fireground usage.
Tests are presently being conducted on a waist harness and a short nylon rope (with a 5000-pound breaking strength) that are intended for the personal use of each fire fighter.
