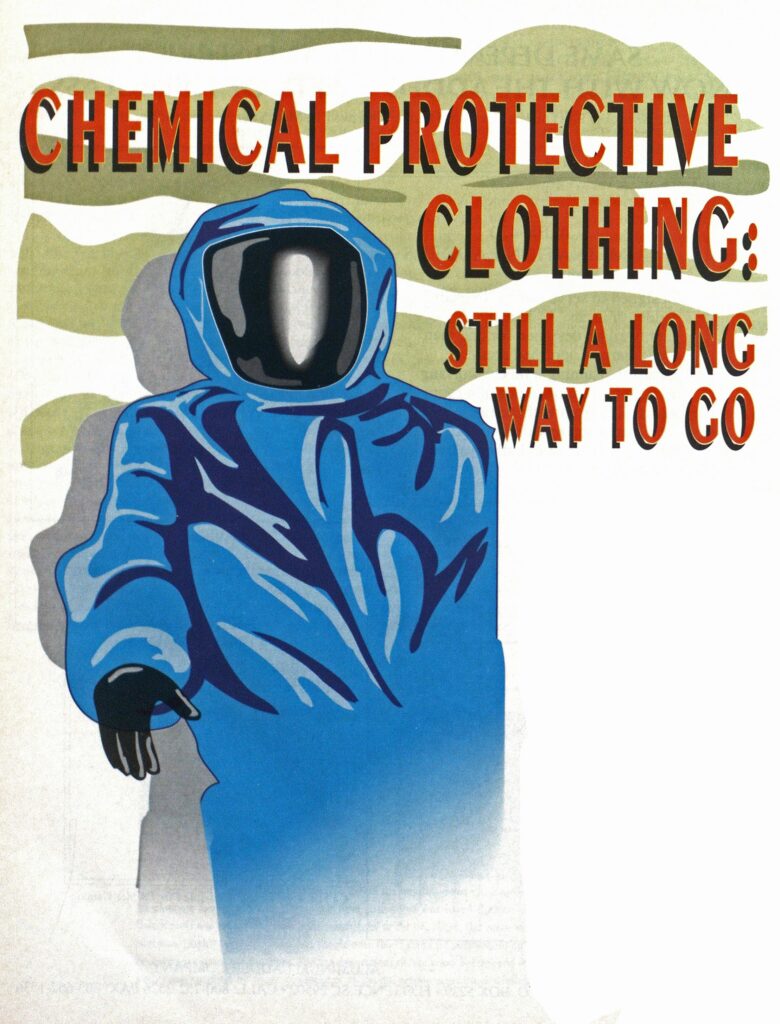
CHEMICAL PROTECTIVE CLOTHING: STILL A LONG WAY TO GO

Technology as it relates to hazardous-materials response is changing daily. In many cases, by the time a body of educational information on hazardous materials reaches the trench firefighter, it already is outdated. The firefighter’s role as a haz-mat responder still is evolving, and so, too, is the protective clothing and gear for these responders. The overall status of chemical protective clothing, as I see it, presents us with a real dilemma when it comes to selecting suits to be worn for haz-mat operations. At this point in time and technology, for example, there is no one suit material that is resistant to all the chemicals that could be encountered by haz-mat responders.
NFPA STANDARDS
On February 5, 1990, the National Fire Protection Association Standards Council adopted NFPA 1991 Standard on Vapor Protective Suits for Hazardous Chemical Emergencies, NFPA 1992 Standard on Liquid Splash Protective Suits for Hazardous Chemical Emergencies, and NFPA 1993 Standard on Support Function Protective Garments for Hazardous Chemical Operations. Although these standards are designed to govern the manufacturer and protect the end user, there still are many questions to be answered when choosing a chemicalprotective suit.
You should begin the selection process by becoming thoroughly familiar with each applicable NFPA standard. Among the things you will discover is that some of the NFPA 1991 certified vapor protective suits were certified with the addition of a vapor splash overcover. The ensemble would not have passed the testing criteria for the specified battery of chemicals without the overcover.
If the NFPA 1991 certification was gained in this manner, then the overcover becomes an integral part of the certification. With liability in mind, you cannot violate the certification by removing the outer cover. The extra layer, however, could represent a potential heat-stress situation in an environment where fire is not a consideration. So, the garments that have gained NFPA 1991 certification without the overcovers will have to be seriously considered not only from a financial aspect but also from a health and safety standpoint.
Another thing you see when reviewing the standards is that NFPA 1991 states: “This standard does not apply to protective clothing for any firefighting applications, and does not provide criteria for protection from radiological, biological, or cryogenic agents or against flammable or explosive atmospheres.” Considering this statement, are you satisfied that the nature of your next chemical response will conform to the safety criteria written into this standard?
Problems such as these must be addressed so that the life span of the emergency responder might be extended. Regulations, codes, and laws to enforce protective-clothing safety standards are overdue, and it is time for the fire service to push the appropriate agencies in that direction.
SEARCH FOR DATA
As hazardous-materials officer for the Submarine Base Fire Department in Groton, Connecticut, I, several years ago, had to select chemical protective clothing for our department. Before 1 could make such an important decision, I had to identify the hazards most likely to be encountered in our response district. 1 found that many different types of hazardous materials, some in bulk quantities, were present in our industrialized jurisdiction. Many of these chemicals are common in nature, and some are exotic and extremely unique. After completing the monumental task of identifying the chemicals, I began to investigate the chemical protective clothing available. 1 found many different barrier materials and designs available in a variety of levels of protection. This comprehensive evaluation process sent my inquiries in many different directions. I asked many questions, which sometimes were answered vaguely and inconsistently by manufacturers and their representatives.
For example, I contacted a manufacturer with regard to a synthetic fiber/coated suit that did not have heat-sealed seams. Concerned about the chemical protective integrity of this particular design, I asked about the rather large stitch holes I could see through when holding the garment up to the light. The company’s chemical suit technological specialist told me that the molecular structures of the most commonly encountered chemicals made the chemicals too large to pass through such small holes.
This type of answer prompted me to investigate further, and I found that there was a dangerous lack of credible information in this area. While attending the Great Firehouse Expo in Baltimore in 1987, for example, 1 stopped at a booth displaying chemical protective clothing to determine whether there might be some new developments of which I was unaware. I asked what the manufacturer had to offer for flashover protection for use with its Level “A” suit, now called the vaporprotective suit. I was referred to an overcover whose coating, the factory representative assured me, contained a special additive that was extremely fire resistant and effectively would handle a flashover condition. I asked for some printed data to back up this claim, and he handed me the manufacturer’s guide for the garment.
At a chemical protective manufacturers’ discussion panel presented during another convention, several of the leading manufacturers’ representatives fielded questions from attendees. One of the representatives was asked about the shelf life of its synthetic polymer suit. He told the audience of approximately 600 that “the chemical resistance gets better with age due to the … coating’s crystallizing and becoming harder.” He also stated that “based on this, shelf life was not of any major concern.”
My growing impression that we needed more guidance relative to selecting chemical protective clothing was confirmed when I was preparing to present a 16-hour hazardousmaterials overview course at a local fire department. While developing the customized training course, 1 evaluated the hazardous-materials equipment the department had on line so that the training would be more relevant to its needs. I found that approximately 12 months before, the department had purchased two vapor-protective suits. When I requested the manufacturer’s chemical resistance data for these suits, the fire chief stated that he had not received any data for the “butyl” suits. My efforts to obtain these data from the manufacturer seemed to open up a Pandora’s box. It turned out that the suits sold to this ill-informed fire department were PVC, not butyl. The manufacturer not only was unwilling to provide any chemical resistance data but would not even tell us the material used in the visor.
We later discovered, as part of an investigation by the town attorney, that the manufacturer had not developed any data and had no intention of making a financial commitment for this purpose. The manufacturer then suggested to the department that it buy a new suit it was offering “since it came with chemical resistance data.”
I’m sharing these experiences with you to illustrate some of the complexities that can be involved when selecting chemical protective clothing. Some of the problems, of course, have been improved by the adoption of NFPA 1991, 1992, and 1993 standards (see sidebar opposite).
DO YOUR HOMEWORK
Ask crucial questions and obtain documentation of NFPA certification prior to purchasing chemical protective clothing. Ask questions such as:
- How extensive are the chemical resistance data? Be sure to determine whether the data at least meet your response needs. Check the origin of the data to determine credibility. It is extremely important, for example, to find out if the testing was accomplished by a recognized independent testing laboratory. (NFPA standards require third-party certification, and the symbol of the testing/certifying facility should be on the manufacturer’s label.) If so, you should ask to see the complete test results so that you can determine whether—in the case of variable results—the manufacturer is making you aware of the worst test results as well as the most favorable outcomes. Some manufacturers have a reputation for publishing complete information, including the worst test results; others seem to print anything they believe will move their product.
Also, determine whether the approved ASIM test methods and the ASIM FlOOl Test Battery of Chemicals (which includes 15 common industrial chemicals plus chlorine gas and anhydrous ammonia) were used as the bases for the manufacturers’ published data.
Concern yourself with the entire suit. Sometimes—if the suit is not NFPA-certified—chemical resistance data are obtained by testing only a swatch of the suit’s material instead of the entire suit. Also, protection will vary with the thicknesses of the materials used in the clothing. Determine, therefore, whether the thicknesses of the materials used in the suit are the same as those used in testing.
Be aware also that manufacturers’ literature does not always include all the suit’s components such as the visor, attached gloves, boots, and gaskets. Ask about the availability of resistance data for each of the materials that may be exposed. If these data arc not available, then you must evaluate the overall integrity of the suit if it is to be exposed to any given hazardous atmosphere.
- What are the sources of the data?
- Are breakthrough times and permeation rates included?
Another area of limited information is the Bash protection for vapor-protective suits. There is no standard to govern this type of protection, although studies in this area are underway. When buying suits for this type of protection, determine w hether the overcover design will minimize the chance of combustible and/or flammable vapors becoming trapped inside between the layers of protection. Most flash cover garments offer little or no chemical resistance, and they may have to be discarded after a single use because of the type of chemical to which the material has been exposed.
Visor. Another important question to ask is. How is the visor attached? In some cases, an exposed natural rubber gasket was used to seal the visor to the suit barrier material.
Seam stitching. Check to see if the seams are stitched. If so, is the stitching of the seams exposed? Or is it sealed by some type of strapping, heat, or an adhesive? If adhesives were used, are they compatible with the chemicals on the resistance chart?
Design ancl closures. Once you have determined that the garment has chemical integrity, evaluate its design and closures. Are the boots and gloves permanently attached or are they field-replaceable? Does the sleeve of the garment allow the wearer to extract his or her arm to the inside of the suit to adjust the SCBA or tend to other emergencies? Choose the model most suited to your department’s needs. A front-entry suit, for example, may fit your needs, but if your responses might bring you to a directsplash situation, a rear-entry suit would be safer.
Operating temperature range. Once your inquiries relative to resistance and design have been answered to your satisfaction, turn your attention to the operating temperature range of the garment. This could be a critical factor for departments operating in colder climates. Even if your department is in a warmer region, you must consider the storage temperature of the chemicals inherent to your response district.
STORAGE A PRIME CONSIDERATION
Ask the manufacturer how to store the suit and w hat its shelf-life expectancy is. Some suits must be stored flat or hung upright in a cool, dry atmosphere, while others can be stored in ftberboard drums, rolled, folded, and stored in hot-cold or light-dark environments. Take into consideration your facility’s storage capability and the availability of space on your response vehicle. Storage methods could be especially pertinent to the performance of the suits.
After use or an extended period in storage, the suit must be tested to verify that its resistance qualities are intact. Most of the reusable suit manufacturers recommend some type of outward leakage test after a predetermined time of storage.
Ask the manufacturer how often the suit should be tested and the methods that should be used. Several test methods such as visual inspections, light bar tests, soap bubble tests, and the widely recognized outward leakage test have been used by end users in the field. A company in my area offers an inward-leaking test that involves having a response team member wear a vapor-protective suit in a chamber into which a corn oil mist is introduced. The wearer then is instructed to perform a series of movements that simulate the movements most commonly made during an incident entry. The interior atmosphere of the suit is monitored during the exercises to determine whether there is any inward movement of the exterior atmosphere.
WATCH THE REUSABILITY FACTOR
Beware of the limited-use garment sales pitch! Some vendors may maintain that their garments can be used for five hazardous-materials incidents before being discarded. I have difficulty with such a claim because often the vendor does not stipulate the type of exposure (vapor or direct splash, for example) or the limits of the contamination on which the claim is based. Some manufacturers provide extensive resistance data, while others leave something to be desired when it comes to providing data.
As noted, organized efforts to influence agencies to introduce legislation that will make the job of the haz-mat responder safer are needed, especially because unprotected exposures to hazardous materials can cause insidious and serious consequences for responders.
Many of us with some time on the job have experienced muscle strains, sprains, perhaps a broken bone or two, and maybe burns—which in most cases eventually healed. When it comes to damages caused by exposure to a hazardous material, however, we get only one chance—and that is to prevent the exposure. We must stay clean because these chemicals don’t simply wash off.