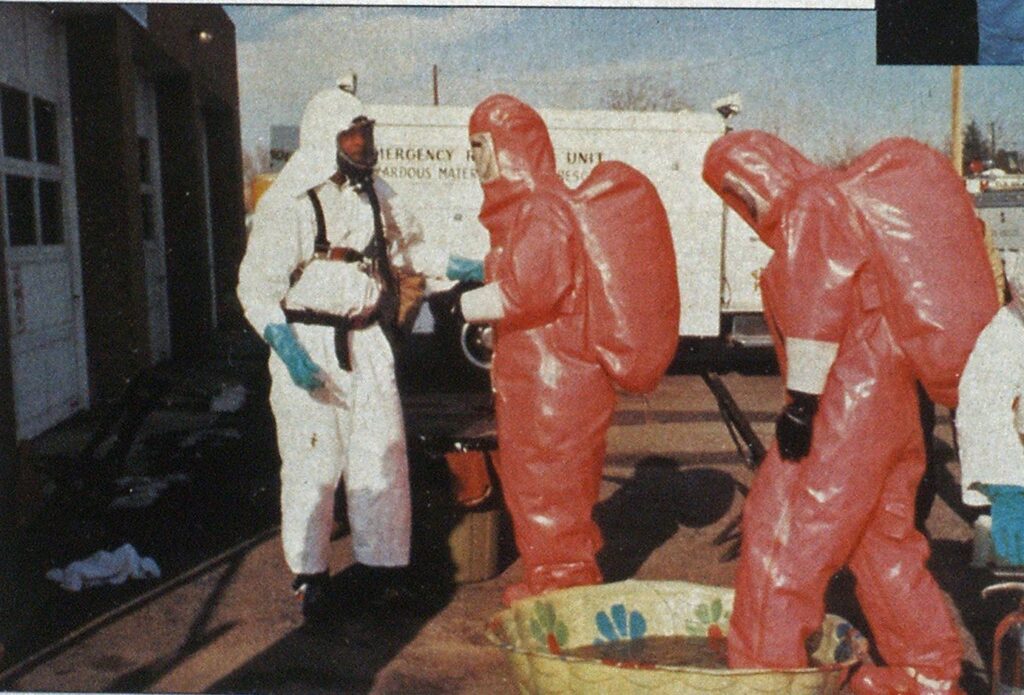
Decontaminate! A Perspective For First Responders
FEATURES
HAZARDOUS MATERIALS



Photos by Steven P. Maslansky
Contamination avoidance is the best posture to adopt at a hazardous material (hazmat) incident. However, in many instances personnel and equipment are inadvertently or unavoidably contaminated in a number of ways, including:
- Exposure to vapors, gases, mists or particulates in the air;
- Splashing by materials during size-up/investigation, suppression or containment;
- Walking or driving through liquids, powders, or contaminated soil or vegetation;
- Utilizing contaminated instruments or equipment;
- Skin contact with contaminated personal protective equipment (PPE) or clothing;
- Transporting contaminated personnel.
Recently, a suburban New York fire department responded to a transformer explosion and fire. Responding personnel and apparatus were contaminated by the subsequent spill and smoke, which contained PCBs (polychlorinated biphenyls) and their combustion products of dioxin and di-benzo furans. Unknown hazards, as well as unclear protocols and decontamination procedures resulted in having to dispose of affected turnout gear and portable radios. Three pieces of apparatus and one ambulance had to be removed from service. The cost for decontamination exceeded $50,000.
Decontamination protocols are commonly overlooked at many incidents; they can be defined if several basic concepts are realized.
Decontamination (decon) is a process by which a hazard, whether it be chemical, biological or radiological in nature, is reduced to some predetermined safe level, usually to normal background concentration by removal, neutralization, absorption, chemical degradation, dilution, covering, or weathering.
Decon of personnel or equipment can be broken down into three general categories: environmental decon, safety decon, and health decon.
Environmental decon
This is performed to protect environmental receptors such as soil, air, or water supply, in which low concentrations of a pollutant may have long-term consequences. This is the “part per billion or million” range of contamination.
Safety decon
This is done when a substance is not overly toxic or corrosive, but manifests a property that could cause a safety problem such as slippery walking or riding surfaces. Many mild alkalies and diesel fuel fall into this category.
Health decon
Here the material, by virtue of its toxic, reactive, flammable, or corrosive properties, presents a hazard to the site responder with or without personal protective equipment, or to the responder’s equipment.
Those responsible for decon procedures should, where possible, and with the sometimes sketchy information available, determine both the degree of hazard and degree of risk to which personnel or equipment will be exposed.
Degree of hazard
This refers to the inherent characteristic(s) of the substance that defines it as being hazardous, i.e., flammable, toxic, reactive, radioactive, carcinogenic, corrosive, etc. The degree of hazard is a function of the property of the specific agent, i.e., the type of hazard, its transformation and combustion products, and, most importantly, its concentration. For example, dioxin (2,3,7,8-TCDD) and saccharine are both known laboratory animal carcinogens, but dioxin produces its effects at concentrations of a million times less than those required by saccharine.
Another example would be two pressurized cylinders, one containing carbon dioxide, the other chlorine. Both are hazardous, but chlorine, by virtue of its toxicity at very low concentrations and strong reactivity, presents a greater hazard.
Degree of risk
This is the potential harm that will be done to the responder. It is a function not only of the hazard present but also the probability that the hazard will manifest itself. If the two previously mentioned gas cylinders were of equal integrity, the risk to the responder would be equal. However, if the carbon dioxide cylinder had deformed walls and a defective valve assembly and the chlorine cylinder was intact, then the carbon dioxide cylinder would have a greater risk assigned to it. Risk is a function of:

Photo by Steven P. Maslansky
- Degree of hazard;
- Integrity of the container;
- Its environmental condition at an incident;
- Its splash or fragmentation distance if rupture should occur;
- Likelihood that a responder will come into contact with it.
Along with degree of hazard and degree of risk, the decon officer, team or specialist, or incident commander must consider the physical state of the contamination (i.e., particulate, gas, sludge, liquids, etc.) and the quantity involved. Will responders be contaminated only on the bottoms of the boots or will men and equipment be exposed to large quantities? Those in charge must consider not only the contamination potential of fire and police first responders, but also that of Emergency Medical Service (EMS) personnel handling victims, other responding governmental or contract personnel, equipment onsite or at the hospital, and at an off-site decontamination area (should the fire station or another area be utilized for final cleaning of equipment).
Although obtaining essential information of the specific chemicals or agents involved at a scene is important, such information is not always readily available. Decon stations must be set up prior to or concurrent with commencing onsite operations. It is therefore necessary to select a decon protocol that will cover a broad range of contaminants. Decon protocols can be established for handling generic hazard classes. The general class or classes of materials involved, except for mixed-product or waste incidents, is usually known initially. A protocol can then be selected for decon for general classes, such as corrosives, radioactives, etiologic agents, or class A poisons. The decon protocol initially assumes that personnel or equipment working in the “hot or exclusion zone” are grossly contaminated (see “Establishing Control Zones” FIRE ENGINEERING, December 1983). The decon area (in the warm zone or contamination reduction zone) should be large enough to handle personnel and equipment. Decon activities can later be downgraded as more information is gathered on the type of contamination, its amount, and concentration. The time constraints imposed by the necessity of using protective clothing and adhering to decontamination protocols must always be considered.
Keeping equipment and personnel upwind of the incident site will help to minimize later decon procedures. Likewise, the decon area should be upwind if possible. Covering of monitoring devices, tools, and equipment with disposable plastic sheets and tarpaulins can also minimize subsequent cleaning. Care of course should be taken when placing plastic near hot or moving parts. Likewise, disposable suits may be worn over fully encapsulated suits to minimize decon and extend the wear life of expensive equipment.
In general, wet contamination should be kept wet, and dry contamination should be kept dry. Some dry compounds may form solid oxides when wetted and may be more difficult to remove. It may also form reaction products that may complicate decon procedures.
Decon operations should start with the easiest methods. For example, a general spraying first to remove the bulk of contamination followed by a scrubbing of difficult areas if necessary. Such a procedure will avoid unnecessary contact with highly contaminated areas by decon personnel, who should be in a level of protection equal to or one level below that of the response personnel. Although many response teams have shunned the use of disposable suits for on-site work, such suits for decon personnel are both cost-effective and warranted.
For wet procedures, water can be both an ally and an enemy. It creates unwanted runoff or spreads contamination. Some departments have had difficulty finding a contractor or support agency to collect, treat, analyze or remove their decon wash water. It may be necessary to conduct personnel decon over wash tubs filled with absorbent materials that will be disposed of more easily. However, it is generally good practice to try to limit the amount of water utilized. The use of large wash tubs or small children’s wading pools for decon of personnel can aid in the collection of decon water. Likewise, utilizing small pneumatic garden sprayers as a water source will help minimize the volumes of water employed. Remember, it is not the volume but rather the pressure that does the cleaning. The utilization of a low sudsing-mild detergent will improve wetting action.
Weather is an important consideration during decon operations, as frozen contamination may be very difficult to remove on-site. Wet decon procedures during cold weather can cause operational problems for both personnel and equipment.
For equipment and apparatus cleaning, numerous steam and low and high pressure spray units are available. In general, the lower pressure units (90 to 120 psi) flush off a general or special decontamination or neutralizing solution at a rate generally from 5 to 30 gpm. With higher pressure units (up to 5,000 psi) decon or neutralizing solutions are normally not needed. Likewise, hot water (120 to 180°F) is normally unnecessary when utilizing the higher pressure units. Many response teams have found that units operating at 500 to 800 psi, with a flow rate of 3 to 5 gpm, to be highly satisfactory. Many departments already have suitable units in-house “disguised” as shop cleaning equipment or hydrant thawing apparatus.
Continued on page 20
Continued from page 18
High pressure or steam cleaning operations can produce contaminated aerosols that can migrate away from the decon area. The utilization of tarpaulins or tents, or modifications of existing on-site structures can both help control fugitive emissions and help mitigate adverse weather effects.
As stated above, hot water and a low sudsing-mild detergent are the decontaminants of choice. However, in some cases it may be necessary to utilize a special solution or combination of solutions containing solvents, bleaches and/or neutralizing chemicals to effect a thorough decontamination. It is important that whatever decontaminant is utilized, its possible reactivity and suitability for the hazardous materials involved must be carefully evaluated. It must be remembered that not all decontaminants are compatible with each other. It is imperative that decon personnel understand the potential hazards of the contaminants, as well as any hazards associated with cleaning equipment or special decon solutions.
It is important that all portions of the equipment and apparatus, including the undercarriage, chassis, and cab, be thoroughly cleaned.
Air filters on equipment utilized in or around the hot or exclusionary zone, where releases have taken place, should be considered highly contaminated, removed, and replaced prior to leaving the scene. Porous items such as wooden truck beds, cloth-jacketed hoses, wooden handles, and, in some cases, turnout gear and leather helmets cannot be properly or cost-effectively cleaned.
Because of departmental protocols, lack of facilities, union involvement, etc., many response teams do not decon other than preliminary field washing.
These departments have had to contract with private licensed hazardous material management firms for equipment cleaning at increased expense. As a result, gear may be out-of-service for several days to a few weeks. Under some circumstances such standard procedures may be an unnecessary burden and expense, and the response units may not have control or a guarantee over the thoroughness or quality of the off-site decon.
Decontamination (decon) is accomplished by removal, neutralization, absorption, chemical degradation, dilution, covering, or weathering.
In addition, many response teams have access to portable personnel decontamination units. Some of these units are nothing more than a box trailer with sinks, toilets, and showers that are set up for personal hygiene; initial decon takes place outside of the unit. Some units are much more sophisticated, with negative atmospheric pressure maintained inside the unit, allowing for complete and safer decon. Unfortunately, these units are expensive ($7,000—$40,000). Research is also underway on special “dry” decon procedures, utilizing freon as the decon agent, which can be fully contained and recycled. However, for most departments it will have to be soap and water for now.
It is imperative that decon procedures be practiced. It is advisable that a quick walk-through of decon protocols at the personnel decon station be conducted before personnel go into the hot zone. This will help insure that response personnel have sufficient air to proceed through the decon line.
Should the hazard be downgraded, and cleaning and removal stations deleted, personnel should be notified prior to returning to the hot zone. All personnel protective clothing and equipment, particularly self-contained breathing apparatus (SCBA), should be thoroughly inspected for signs of wear or defective items.
A question often asked is which agency should be responsible for decon. In many areas the fire service takes the lead; elsewhere the EMS is responsible. EMS personnel may claim that because of their medical knowledge they are most sensitive to personnel decontamination. However, they may not be familiar with the special items of protective clothing, tools, and equipment utilized by the responding fire services. EMS personnel not assigned to the fire services and responsible for decon may require considerable duplication of protective equipment for decon operations that may rarely be utilized. Such utilization without constant training could lead to inadequate safety precautions. At large incidents many times the environmental agencies will be responsible for decon operations. Sometimes they are more knowledgeable of special procedures and sensitive to environmental constraints and disposal procedures.
Ideally, decon should be planned by all the agencies involved, drawing on expertise from each source. In reality, this may be impossible to achieve unless the response team consists of personnel drawn from different agencies, or unless detailed planning prior to response incidents has been conducted.
Because hazmat is fairly new to first responders, many officers and men have not been sensitized to the needs of properly assessing potential hazards and the proper procedures to mitigate such hazards. Although a healthy respect for hazmat situations is a must, overreaction to incidents should be avoided. Continual overreaction to incidents could result in the downplaying of decon procedures when they are really needed.
With proper training and preplanned protocols, decon procedures can run smoothly while ensuring protection of response personnel and equipment as well as safeguarding the environment.