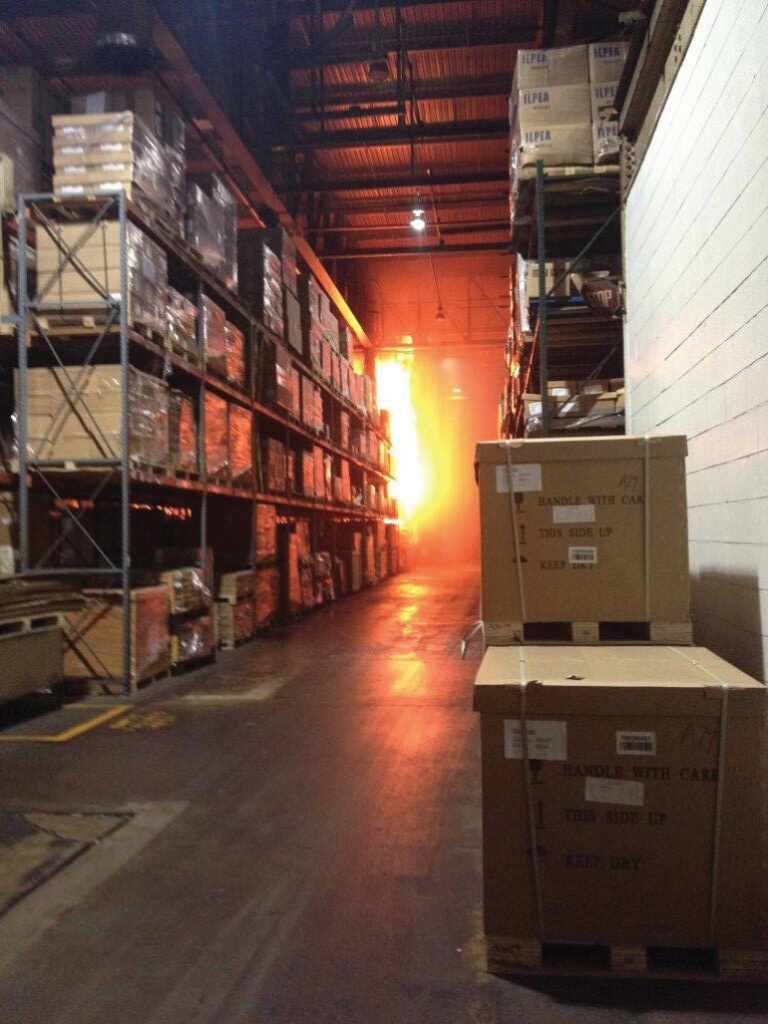
BY ROBERT DUVAL
On April 3, 2015, in the midst of some of the worst weather the region had experienced in several years, a fully sprinklered storage warehouse on the property of General Electric (GE) suffered a catastrophic fire. The entire building was destroyed, as were the contents of appliance parts. Immediately after the fire, members of the Metro Arson Squad of the Louisville (KY) Fire and Rescue Department began to ask how and why an occupied warehouse could suffer such a large fire. The commander of the Arson Squad requested that the National Fire Protection Association (NFPA) assist with its investigation into the circumstances leading to the fire. I traveled to Louisville shortly after the fire and spent several days with the investigators on the fire scene.
![This photo, taken by an evacuating employee, shows the fire in an incipient stage at the end of a row of racks. [Photo courtesy of the Louisville (KY) Metro Arson Squad.]](https://emberly.fireengineering.com/wp-content/uploads/2018/10/1810FE_Duval-p01.jpg)
(1) This photo, taken by an evacuating employee, shows the fire in an incipient stage at the end of a row of racks. [Photo courtesy of the Louisville (KY) Metro Arson Squad.]
Building
The fire building, known as Appliance Park-6 (AP-6), was a 700,000-square-foot structure located in the GE Appliance Park, a roughly 900-acre complex that has been home to GE’s appliance division since the 1950s. The remainder of the complex consisted of seven large manufacturing and storage buildings and 30 smaller structures.
AP-6, built over the period of 1957-1968, was constructed on a steel frame with masonry and metal panel walls, a corrugated metal roof, and a built-up roof covering of insulation and asphalt. The building stood approximately 30 feet high.
The building was originally used to manufacture air conditioners, but over time manufacturing operations inside the space shrunk until more than 85 percent of it was used for storing appliance parts, everything from metal nuts and bolts to plastic hoses and rubber belts. The parts were stored in cardboard boxes or plastic cartons that were either arranged in solid piles up to 12 feet high or on wooden pallets in 24-foot-tall single- and double-row racks with eight-foot-wide aisles. A portion of the structure was arranged as office space along the eastern side of the building.
Fire Protection
Fire protection on the property consisted of a network of underground mains supplied by a series of manually operated pumps drawing water from tanks and on-site reservoirs. The pumps were a combination of gasoline- and electric-powered units used for both process and fire protection water within the complex. The operation of the pumps was monitored and maintained by the staff of the boiler house and the Mill Water building (constantly attended). In the event of a demand (process or a water flow within the fire protection system), an operator would start pumps to meet the demand. There were also 11 hydrants on site supplied by the domestic water system. However, these hydrants were not maintained by the water authority; they were on private property and found to be in disrepair at the time of the fire.
Sprinkler protection within AP-6 was an ordinary-hazard type arrangement with 165° upright sprinkler heads on 130-square-foot spacing per head, supplied through multiple risers around the perimeter of the building. No in-rack sprinklers were installed in the rack storage areas.
This protection was adequate for the manufacture of appliances (when installed in the 1950s). As the occupancy of the building changed gradually from manufacturing to storage, this protection became inadequate. The higher challenge posed by the rack storage of materials of various compositions (plastic, rubber, synthetic, metal) in corrugated containers required a much stronger sprinkler design, including in-rack sprinklers for some storage configurations.
At the height of production, Appliance Park had its own on-site fire brigade. In addition to responding to fires and other emergencies on the property, the fire brigade conducted inspections and testing of fire protection equipment. The facility maintained a self-inspection process for several years. Unfortunately, the fire brigade was phased out in the years before the fire, and inspections of fire protection systems transitioned to the security forces and outside contractors. Fire alarms, including water flow alarms, were monitored by the on-site security force. Because of the self-inspection status of the facility, the local fire department, the Okolona (KY) Fire Department (OFD), did not conduct any on-site inspections prior to the fire.
Weather
In the hours before the fire, up to nine inches of rain fell in the Louisville metro area. This deluge led to localized flooding and kept the area fire departments extremely busy with rescues, electrical hazards, and other emergencies.
The Fire
April 3, 2015, was the Friday before Easter Sunday, and staffing was light throughout the complex, including AP-6. Employees discovered a small fire in AP-6 at the end of an aisle of rack storage in the north center portion of the building at approximately 6:49 a.m. Employees within the building made two 911 calls reporting the fire in AP-6 (photo 1). These calls were followed by a call from the GE security office reporting a water flow alarm from the building.
The regional fire department dispatch center dispatched a first-alarm assignment to the GE complex at 6:51 a.m. based on the information it was receiving from the facility. Since many of the fire departments in the first-alarm response area were tied up with storm-related responses, the dispatch center had to modify the assignments to fill out the run card.
Security contacted the Mill Water Building and the boiler house and requested that they activate pumps, as was the procedure for a water flow alarm. As personnel attempted to start pumps in a sequence, one malfunction after another occurred, and the pumps were unable to maintain sufficient pressure in the fire protection mains for the sprinkler protection and fire department hose streams.
OFD Car 8006 (Major Jody Craig) arrived on scene at 6:59 a.m. and reported heavy smoke showing and, a few minutes later, heavy fire showing from inside the building. Engine 5551 arrived at 6:59 a.m. as well. As additional units continued to arrive, Command requested a second alarm at 7:04 a.m., followed by a third alarm at 7:07 a.m.
During the first few minutes of the suppression efforts, attempts were made to enter the building, but they were quickly abandoned based on the heavy fire throughout the building. A video from a firefighter’s helmet camera, made available to the fire investigators, showed a large volume of fire at the ceiling traveling rapidly from east to west. Command made the decision to fight the fire from a defensive posture at 7:09 a.m.
As units continued to set up for master stream and aerial devices, acquiring adequate water supplies was becoming a problem. Several hydrants on the property were out of service. Problems continued in getting more than one pump online to boost pressure and volume in the fire protection mains on the property.
A localized collapse occurred in the building at 7:18 a.m. This was the first of several collapses within the building over the course of the firefight. A fourth alarm was requested at 7:23 a.m., followed by a fifth alarm at 7:45 a.m. At 7:49 a.m., a box alarm assignment was requested from the Louisville Division of Fire and Rescue to supplement the apparatus already responding and on scene.
A representative of the Louisville Water Authority was requested to come to the command post at 8:12 a.m. The command team decided that to extinguish the fire, it would be necessary to go off the property to obtain sufficient water from the local domestic gridded system in the area surrounding the complex. Additional engines were dispatched to the fire to lay approximately 15,000 feet of large-diameter hose to several hydrants outside of the property. Once these evolutions were completed, sufficient water supplies were maintained, and the fire was placed under control several hours later. Extensive overhaul continued for several days, as the investigation into the cause of the fire began. Because of the distance between nearby buildings, there was no damage to any of the surrounding buildings.
Investigation
Members of the Louisville Metro Arson Squad arrived on scene during the fire suppression efforts and began to gather information on the circumstances surrounding the discovery of the fire and the difficulty the fire departments had in extinguishing the fire because of the lack of a water supply and the apparent ineffectiveness of the sprinkler systems. The NFPA assisted the investigation team in deciphering the sprinkler system and water supply requirements for the occupancy of the building.
The investigation team initially looked into what impact the weather had on the fire, including any lightning strikes in the complex area and rain water seepage into electrical systems.
Another focus of the investigation was the metal halide lighting systems in the building. Investigators collected lightbulbs from throughout the building to compare with the remains of bulbs and fixtures in the area where the fire was first discovered.
Investigators searched for evidence of an incendiary fire as well as the careless disposal of smoking materials.
The investigation team eventually reported the cause of the fire to be “undetermined.” The reported dollar loss from the fire was $50 million for the structure and $60 million for contents.
Managing Change
The changing of an occupancy within a building is a common occurrence. Unfortunately, if the fire protection within the building does not change along with the occupancy, this can result in a dangerous situation. In the case of AP-6, the change from manufacturing to storage occurred over several years. However, the sprinkler protection remained the same, leading to inadequate protection when a fire occurred within the rack storage area of the building (photo 2).
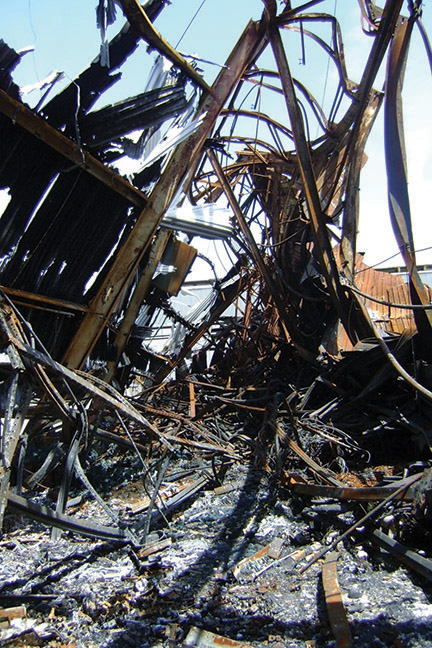
(2) The rack storage area in AP-6 was completely destroyed. (Photos 2-4 courtesy of the National Fire Protection Association.)
This fire is an example of what can go wrong when fire protection does not keep up with the hazards within a building. When an occupancy change occurs, a corresponding change in fire protection systems may be needed to meet the new hazard. These changes are often overlooked by building owners, occupants, and employees. Fire inspectors and insurance company engineers often discover the changes that can impact fire protection.
Witnesses interviewed by fire investigators reported sprinklers operated in the incipient fire area. However, the fire continued to grow unsuppressed until it involved the entire building. The helmet camera video taken by the firefighter from just inside an exterior door shows the fire spreading rapidly across the ceiling of the building above the rack storage, basically unimpeded by any sprinklers. This rapid fire spread can be attributed to the lack of an adequate water supply and a sprinkler system design that could not meet the demand of rack and solid pile storage of several categories of materials (photo 3).
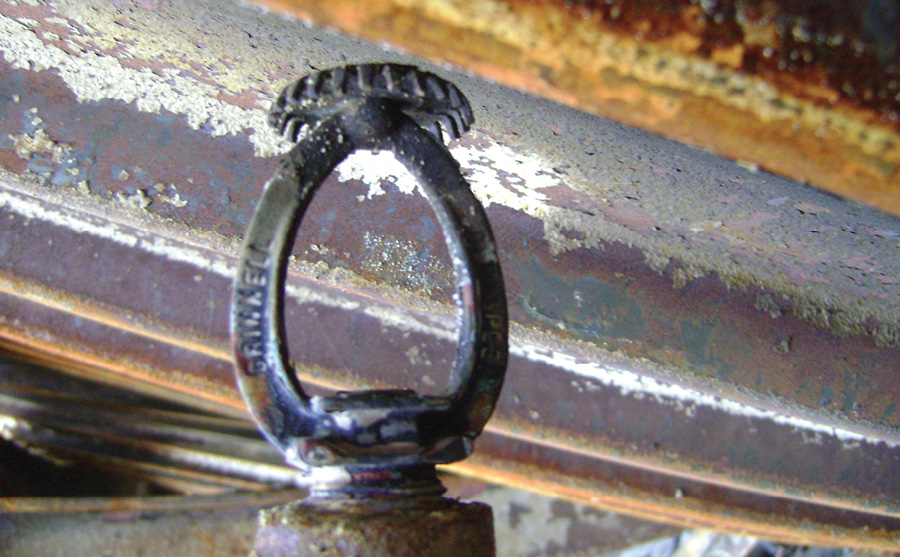
(3) A fused sprinkler head within the rack storage area in AP-6. During the investigation phase, every located sprinkler was found fused.
At the recommendation of its insurer, GE was in the process of a fire protection system upgrade, including replacement of the mill water pumps and a large number of the underground fire protection water mains. Unfortunately, this work was not completed at the time of the fire.
Fire departments should make every effort to stay aware of changes in occupancy (processes, storage, materials, and so on) in facilities within their response district. Accomplish this with prefire planning or regular facility tours. Another way to track changes, subtle or drastic, is through a plan review and permitting process. If a fire department does not have the resources to analyze such changes, it can work with the facility (and its insurer) to review fire protection systems to see that they match the occupancy and the hazards that the occupancy presents (photo 4).
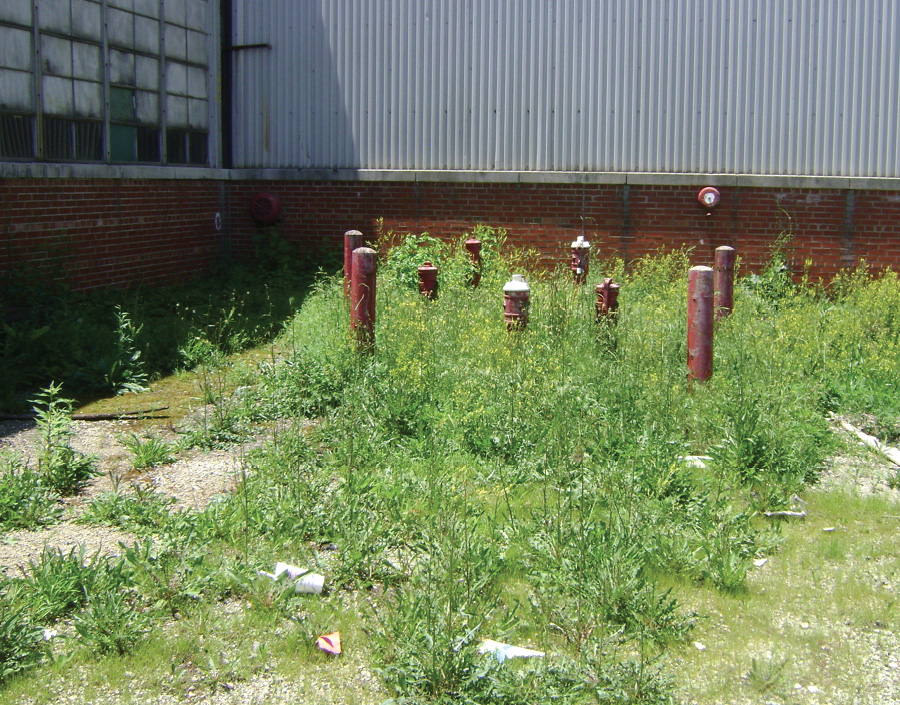
(4) These post-indicator valves, outside of AP-6, controlled the fire protection water supplies for the complex and the building.
Cost is often a barrier to increasing or changing the protection to meet the challenges posed by a new occupancy, process, or storage class. If that is the case, the fire department should work with the building owner/occupancy on options, alternatives, or time frames to meet the challenges. Insurance carriers work with their insured on this topic frequently. Involving the local fire department in this process can lead to better cooperation and risk and change management.
After the fire and the subsequent investigation, AP-6 was demolished. The plot is now maintained as a green space on the complex property.
In 2016, the Haier Group Corporation, a Chinese consumer electronics and home appliance company, bought GE’s appliance division and now owns Appliance Park, which continues to be staffed by GE employees. The OFD indicated that the complex’s water-based fire protection systems are nearly completed and that the fire department meets with management quarterly to discuss fire safety.
Robert Duval is senior fire investigator for the National Fire Protection Association and northeastern regional director for code adoptions and training. He was a member of the FEMA Building Performance and Assessment Team (BPAT) that studied the World Trade Center disaster in 2001 and was involved in the 2003 investigation of the Rhode Island nightclub fire that killed 100 and the Hartford, Connecticut, nursing home fire that claimed 16 lives. Duval is the chief of the Atwood Hose Fire Company in Wauregan, Connecticut, where he has been a member since 1981. He has been an emergency services dispatcher in a regional fire department dispatch center in northeastern Connecticut since 1986 and is an instructor at the Eastern Connecticut Fire Training School. He retired from the Connecticut State Fire Academy after 20 years as a staff instructor. He is a communications specialist for CT-TF1 and a member of the CT IMT-4. He has a bachelor’s degree in mechanical engineering technology from Northeastern University in Boston, Massachusetts.