
BY MICHAEL N. CIAMPO
Ride around anywhere in your fire district, and you’re bound to come across an older structure being renovated or getting some type of modern makeover. Whether it’s a single-story strip mall getting an ornamental canopy; a private residence getting a tile, stucco, or field stone makeover; or an older factory having a false facade installed, you will find something. Each installation is different, and many of these renovations can hamper our firefighting tactics or could lead to a catastrophic event if we operate around them without knowledge of their existence and physical makeup. Firefighters must be more than curious to see the final product and investigate these alterations to see what’s going on and what they might mean to our firefighting efforts. That might mean stopping by the occupancy numerous times to view construction methods; the products being used; and the alterations that severely change the original structure’s layout, hazards, or designed use.
Converted Factory
In your fire service career, you’re going to hear plenty of war stories of years past or one of the other firefighters will point out a specific building and tell you of a previous job they had in there. That’s important to note because if it was a serious fire, what did it do to the building and how was the building repaired? Maybe instead of installing dimensional lumber, the repairs were made with laminated I-beams, metal “c-channels,” or lightweight joists or trusses. Hopefully, someone was able to update the building information records so that firefighters will know this information prior to the next response to that building.
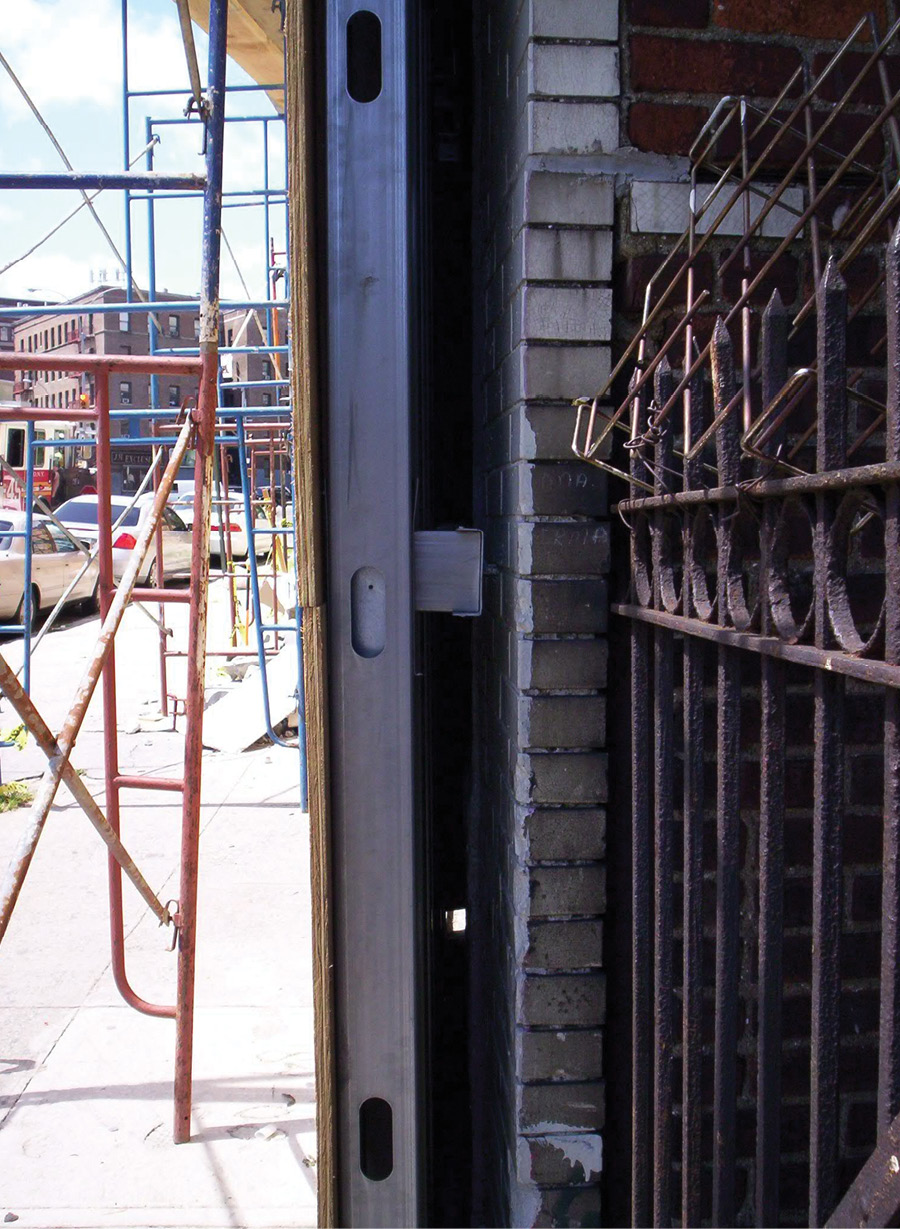

(1) The attachment points are pieces of the metal stud, lagged into the brickwork and screwed into the studs. (Photos by J. J. Cassetta.) (2) The studs run from the ground to the top of the parapet, creating a void between sections. Fire could travel inside this void along the back side of the plywood.
Folklore in our firehouse was that years ago a specific building in our first-alarm district was a jam-and-jelly factory, and there was a small fire in the building. The companies were able to control the fire and limit the damage to the building. After that, the owners were kind enough to drop off a monthly care package to the firehouse for the members to snack on. In the following years, the factory closed its doors and the building became a mix of stores and occupancies—a tire shop, a beauty salon, a nightclub, a grocery store, and a few clothing shops. Years of alterations and homemade renovations that took place inside the building without anyone’s knowledge led to a multiple-alarm fire in the building. After the building sat idle for a while, a company bought it and had some occupancies operating in it before it was intent on renovating the structure; then the building was shut down and all the stores closed.
The old factory is an irregular pie-shaped building that fronts on two streets and has two addresses; and, as luck would have it, it’s built on a steep hill and has three interior levels. The major concern about the structure is its fire load because it is a building supply warehouse and storefront with many combustibles, chemicals, household products, and vehicles stored inside the garage portion on the lower level. Another issue is that the regulations and codes do not require an automatic sprinkler system in the structure. When the occupancy was a factory, fire department units had plenty of access to flow master streams into the building, but the following facelift renovations eliminated that possibility.
Modern Facade
While driving by the vacant structure one day, our unit noticed that scaffolding was being installed along the building. As days went by, we noticed that work was being done on the building; permits were posted and in place at the site. Once the brick work was repointed, most of us assumed that an ornamental cornice, vinyl canopy, or overhang would be installed to give the structure a modern look and that it would resemble most of the other taxpayers in the neighborhood. Much to our surprise, the building, instead, was being wrapped in metal studs from the ground up on three of its four sides (photos 1-2). We investigated how the studs were secured to the building: Would they increase the weight load on the exterior walls or parapet? If so, what would that mean if a fire occurred?
In the front of the building, roll-down gates were being installed, but it was peculiar that the drums, housing, and motor were mounted inside the storefront instead of on the building’s exterior above the opening, which is typical. The mounting position would hamper forcible entry operations by fire department units unscrewing the cover plate over the key-controlled electrical box and operating the limit switches to raise the gates in a fire. In the rear of the building, the roll-down gates had two methods of mounting: The gates on the garage opening were mounted in the same manner as those at the front, and the drums for the doorways were mounted outside above the door frames.
The rear of the building was also being studded as the front and the sides. However, something seemed to be a bit peculiar in the rear. The large old casement windows weren’t being replaced with newer modern energy-efficient windows; the studs ran right over the windows, which could no longer open. The metal walls were now up.
The next stage of the renovation ensued: The building was wrapped in plywood from top to bottom (photo 3). When we saw the wrapping, we realized that we would not be able to apply master streams to the second-floor windows in the rear of the building. The building, fully wrapped in plywood, was then covered with polystyrene insulation, adding more of a fuel load to the new siding. As we watched this new facade beginning to develop, we wondered what would happen if fire vented out of these older casement windows and hit the plywood. We could then have a rapidly spreading fire behind the insulation in the void space or even rapidly spreading along the entire sections of siding (photo 4). Once the insulation was attached, because it was not fire retardant, the upper portion of the building was covered in a concrete-like stucco and the lower section of the building was covered with a man-made, tile-like fire resistive board (photo 5). Once completed, the building was aesthetically very pleasing to the eye and brightened up a once-dreary corner of the neighborhood, but underneath its exterior shell are hazards awaiting firefighters.
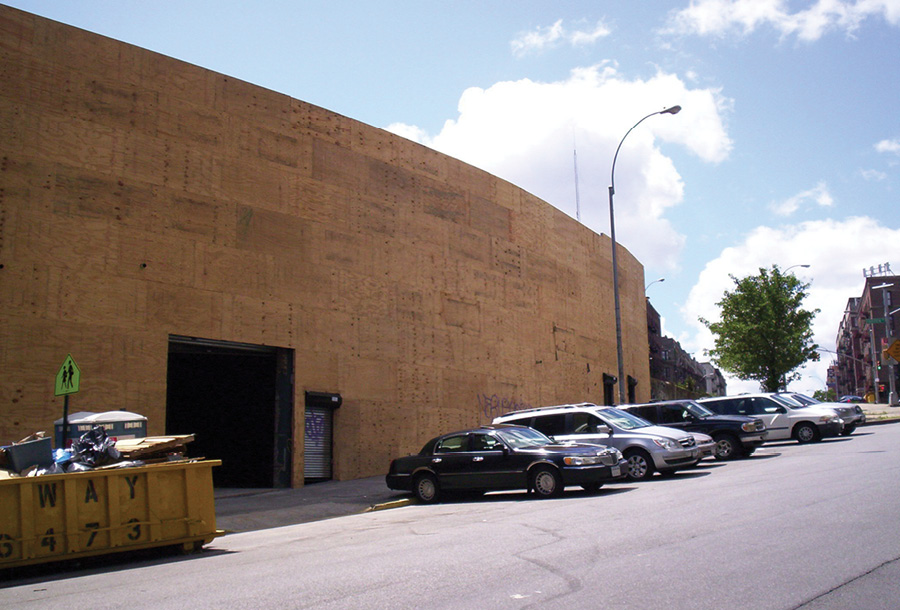

(3) The entire building is wrapped in plywood then polystyrene insulation; the large casement windows in the rear on the second floor are now covered. (4) The rear of the structure is completely encased. Units would have a hard time finding the original casement windows on the second floor.
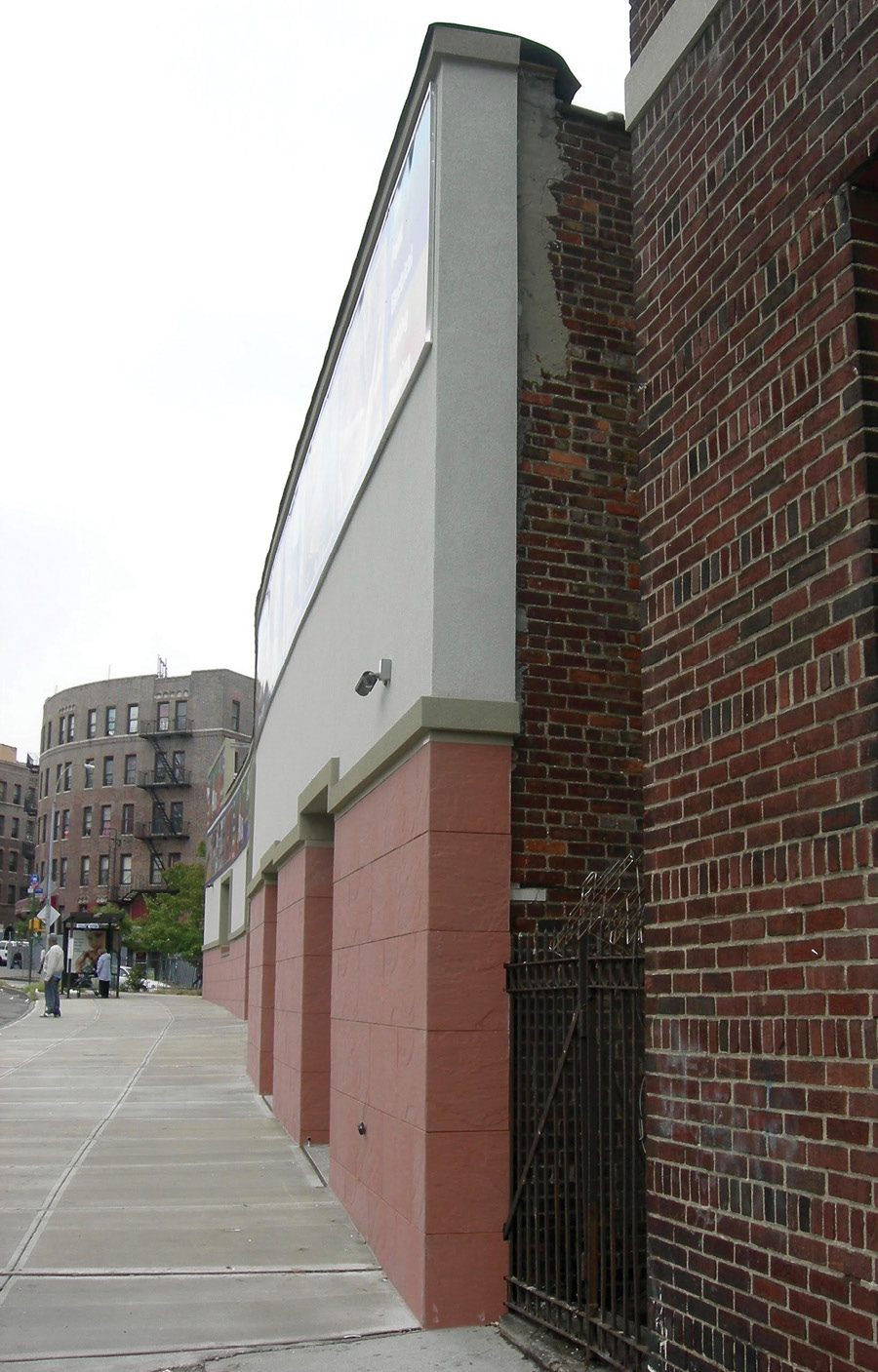
(5) Firefighters unfamiliar with the building might not know its original construction features; a 360° size-up can provide much information to operating units.
Points to Ponder
Following are some safety considerations and precautions applicable to buildings clad in this manner:
- Firefighters continually monitored this major construction alteration and filed building referral reports through the proper channels when questions arose about its features.
- Once the occupancy was open for business, firefighters thoroughly inspected the building to see the layout and features of the structure [tri-level floors, vehicle storage, freight elevator, lumber and other storage racks, flammable liquid storage, and roll-down gate controls (photo 6)].
- Buildings built into a hill can have numerous floors or half-floors, depending on the grade on which they are built. Assigning terminology of which floor is which is crucial for communication between units when a fire occurs in this type of building.
- Buildings fronting on more than one street can carry two street addresses; if you’re submitting response data to a system, be sure to provide both addresses.
- Updates were made to the Critical Incident Data Reporting System so firefighters have the proper and updated information on the building when responding to one of the building’s addresses.
- The building is a high-hazard occupancy in our district; we often bring new members to inspect it or to drill there periodically. Its three-level design, unusual construction features, roll-down gates, and freight elevator that has bi-fold exterior doors are all reviewed.
- A collapse zone is a very important consideration at this occupancy; the false veneer wall could detach from the brick wall if fire were to vent out of the old casement windows and weaken the support structure.
- Place emphasis on having a few means of egress for firefighters operating on the roof performing vertical ventilation in case the siding becomes involved in fire and cuts off their primary means of egress.
- Commercial occupancies such as this require a 2½-inch handline as the initial attack line; units should expect to deploy an apparatus-mounted master stream if the fire begins running the siding.
- Polystyrene insulation is a hydrocarbon-based product, is flammable, and produces a lot of black smoke when on fire. It will also melt and drip down on members operating in its vicinity. All must wear appropriate personal protective equipment.
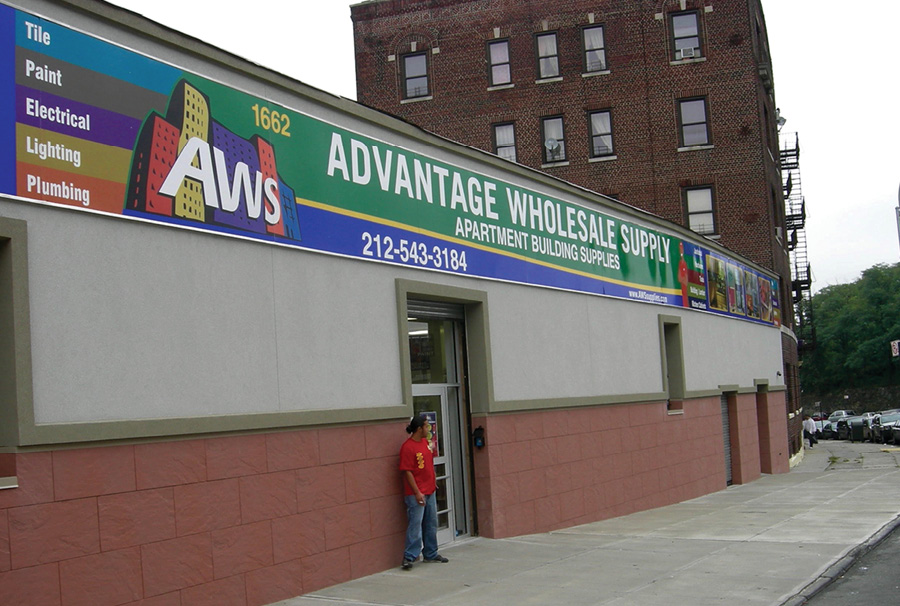
(6) The bottom section of the front wall is a man-made fire resistive tile; the upper portion is a cement/stucco-like product. Note that the roll-down gates are mounted inside the occupancy.
Michael N. Ciampo is a 33-year veteran of the fire service and a lieutenant in the Fire Department of New York. Previously, he served with the District of Columbia Fire Department. He has a bachelor’s degree in fire science from John Jay College of Criminal Justice in New York City. He is the lead instructor for the FDIC Truck Essentials H.O.T. program. He wrote the Ladders and Ventilation chapters for Fire Engineering’s Handbook for Firefighter I and II (Fire Engineering, 2009) and the Bread and Butter Portable Ladders DVD and is featured in “Training Minutes” truck company videos on www.FireEngineering.com.